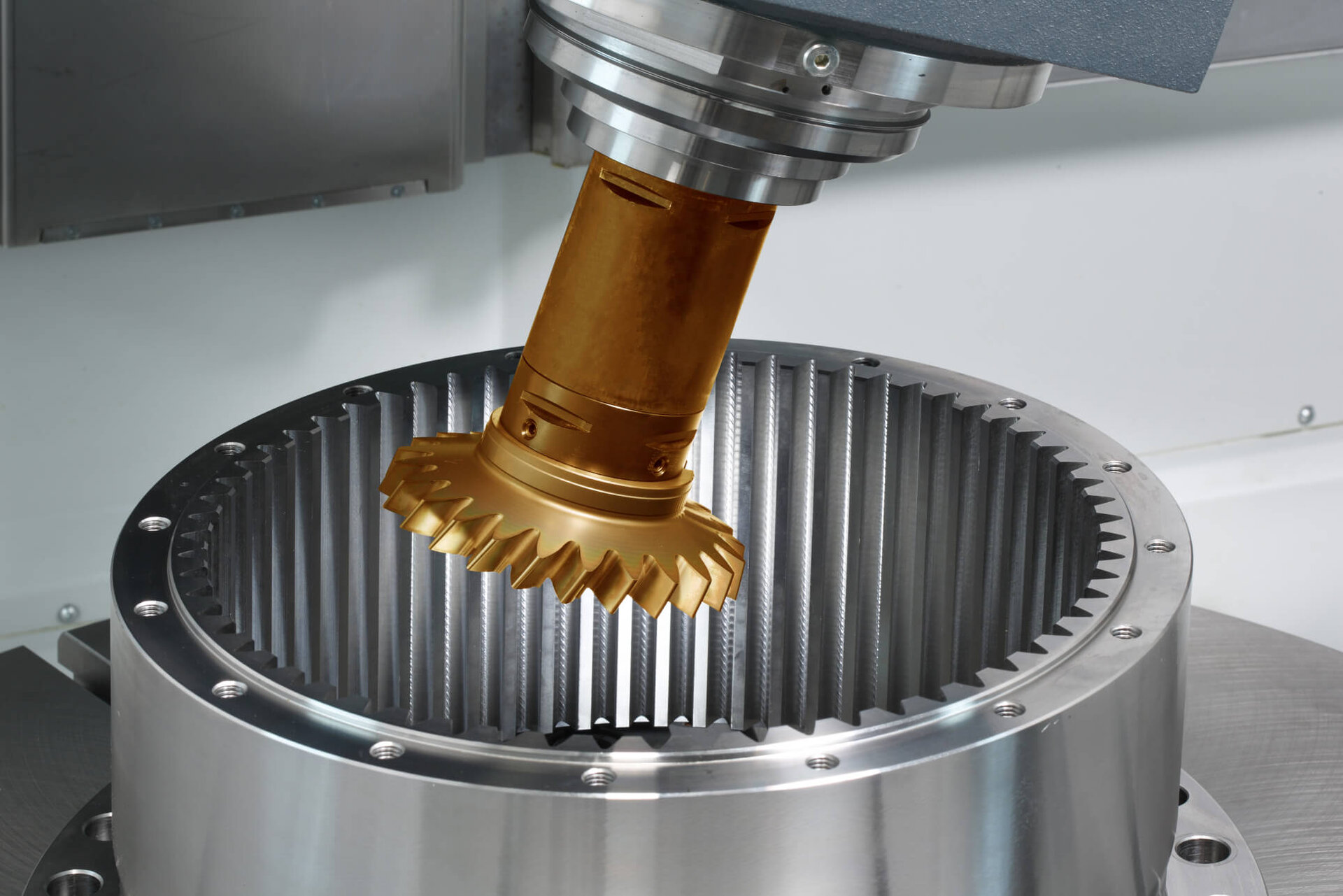
Skiving
So what is skiving?
Skiving is a metal cutting process for the production of gear teeth, based on the patent of Wilhelm von Pittler from 1910. In recent years, thanks to the latest developments in manufacturing technology, the technology has emerged as an efficient and flexible alternative for the gear cutting of workpieces.
Skiving is used for the gear cutting of workpieces with interfering contours and thus replaces gear shaping. The process can be used for both internal and external gearings. In skiving, the workpiece and tool axes work in a continuous process, with the two axes at an angle to each other.
A characteristic feature of skiving is the oblique arrangement of the tool axis relative to the workpiece axis. This is referred to as the axis cross angle. Due to this adjustment of the tool, a defined axial feed and the coupled speed of the tool and the workpiece, a relative movement is created. This relative movement "peels" the tooth space out of the workpiece along the main cutting direction.
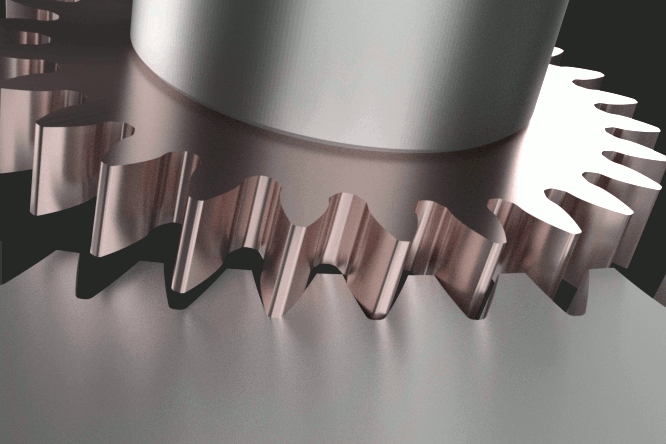
The rapidly changing cutting forces during hob peeling cause the machine and control system to vibrate. Therefore, skiving requires extremely rigid machine structures, tool and workpiece carriers and particularly optimized control loops.
The DVS TECHNOLOGY GROUP has the corresponding machine concepts, assemblies and the control engineering know-how. At Präwema and Pittler we use this know-how to offer particularly efficient production solutions for shaft-shaped workpieces. By using several tool carriers, we can also completely machine workpieces. This is particularly useful for very tight workpiece tolerances in order to avoid errors caused by multiple clamping. Even with small batch sizes, complete machining in one machine is an economical option, e.g. to keep investments in machines low.
Since DVS TECHNOLOGY GROUP also masters tool design and manufactures tools, particularly high qualities can be achieved. During the life cycle of the production solution DVS TECHNOLOGY GROUP supports the continuous optimization of machine, process and technology. In this way we support our customers to maintain and build up their economic advantages and to increase their yields.
Skiving has its advantages in the case of
- Gears with small runouts
- In case of several different toothings on one workpiece, which can be produced with the help of the automatic tool change, which is made possible by the tool being mounted on one side only anyway (e.g. the so-called 'stepped pinions' in multiple planetary stages)
- For internal gears
The kinematics required for hobbing are closer to those of a typical lathe or turning-milling center than hobbing. As a result, hobbing is easier and better integrated into a lathe than gear hobbing, which often requires a double-sided tool that cannot be changed automatically. This means that hob peeling also has advantages in the following situations:
- Complete machining
- For small and medium batch sizes, in each case because of the comparatively easy retooling of a universal machine with automatic tool change
The processes in comparison (pdf 486kbyte)
CNC Machinery Overview
Tools Overview
You have not found the right solution?
Here you will find only an excerpt from our portfolio. If you are interested in other technologies or workpieces or if you are looking for more individual solutions, please feel free to contact us.