With the vertical series of our Präwema SynchroFine, we have created a platform on which main and secondary processes can be individually combined and thus even the complete gear can be produced or machined in the soft and hard state.
Depending on your requirements, the gearing can therefore be produced, for example, in the hobbing process and then be hard-finished on the same equipment after the components have been hardened. For this hard-finishing process, PRÄWEMA can draw on its many years of experience in the internal gear honing process.
The modular design of the SynchroForm V offers an optimal platform to add further modules to core technologies such as hob peeling, internal honing, or dressing.
Thus, optimal references can be produced by adding further processes, such as turning or grinding of bores and face surfaces.
Modular technology platform
Efficient turnkey machining for the gearing of drive components
One or two spindles depending on quantity requirements
Versatile technology bandwidth for precise soft and hard machining
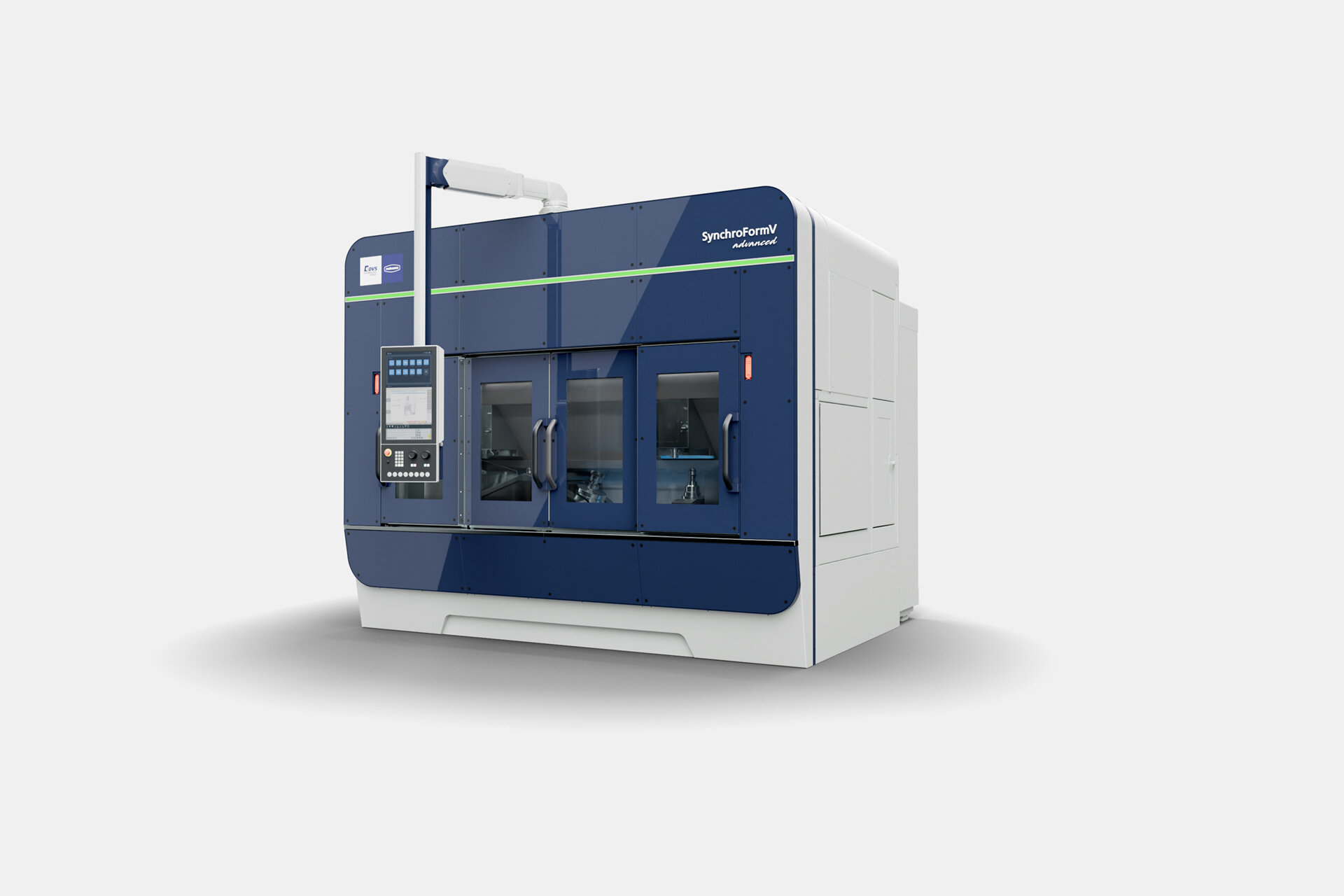
SynchroFormV |
|
WORKPIECE |
|
Max. workpiece diameter (mm) |
300 |
Max. workpiece length (mm) |
290 (center loading) –100 bei (side loading) |
COMPOUND SLIDES |
|
X-axis travel (mm) |
1500–3300 |
Y-axis travel (mm) (WKZ option) |
284–364 |
Z-axis travel (mm) |
330 |
WORKPIECE SPINDLE |
|
Drive power 100% duty cycle (kW) |
35–63 |
Torque 100% duty cycle (Nm) |
75–430 |
Max. speed (rpm) |
6000–10000 |
TOOL SPINDLE |
|
Max. speed (rpm) |
6000–10000 |
Rated power (kW) |
6–42 |
Rated torque |
10–140 |
Mount/interface |
Capto |
*Different workpiece geometries require more individual machine designs. For this reason, the technical data given here serve as a guide, but may deviate from reality in individual cases.