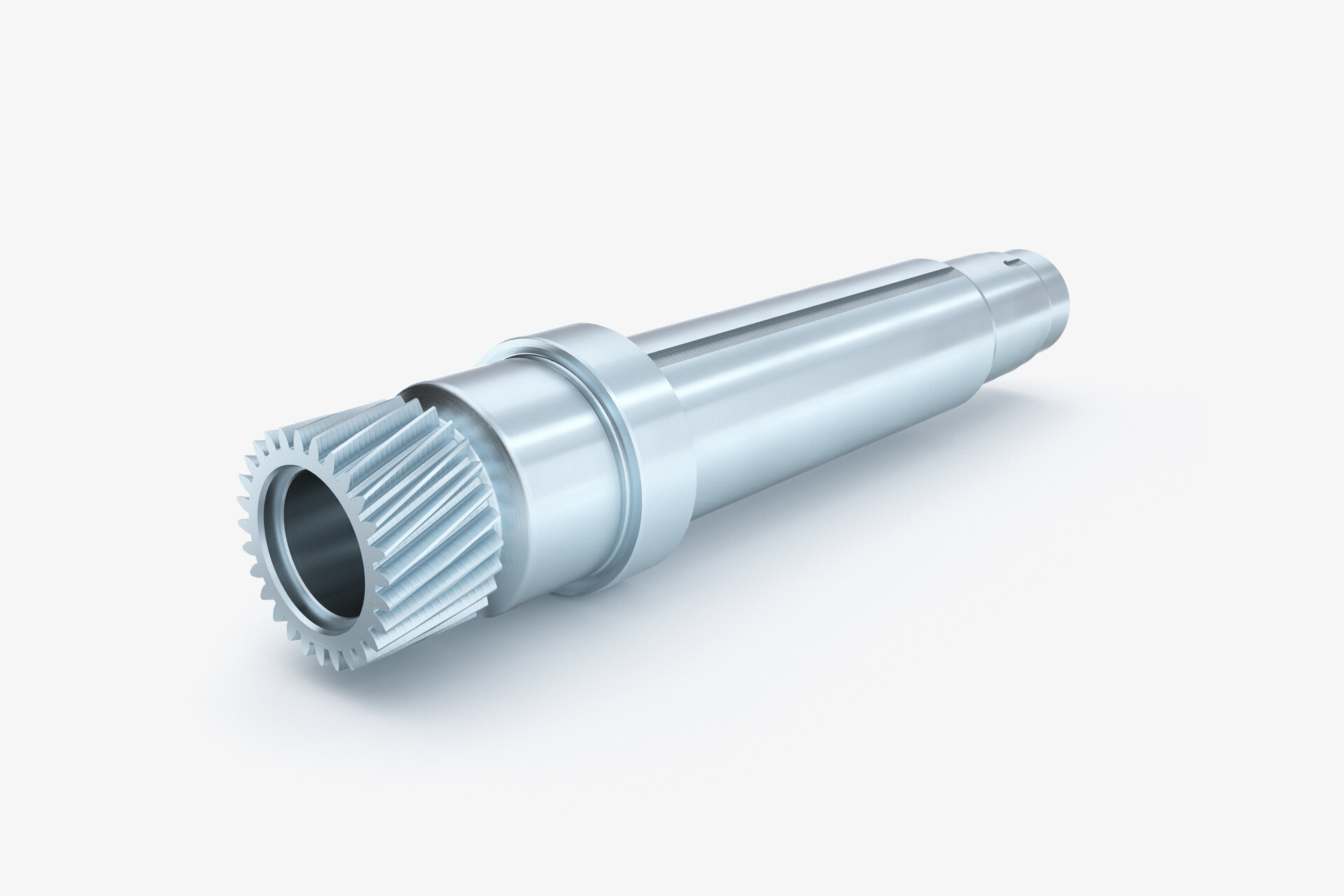
Perfect rotor shafts for electro-mobility
New challenges call for new ideas: The DVS TECHNOLOGY GROUP modular systems fulfill all needs for high quality, efficiency and flexibility. They make the optimal complete solution for perfect rotor shafts in modern electric motors.
Three pillars of future-oriented production
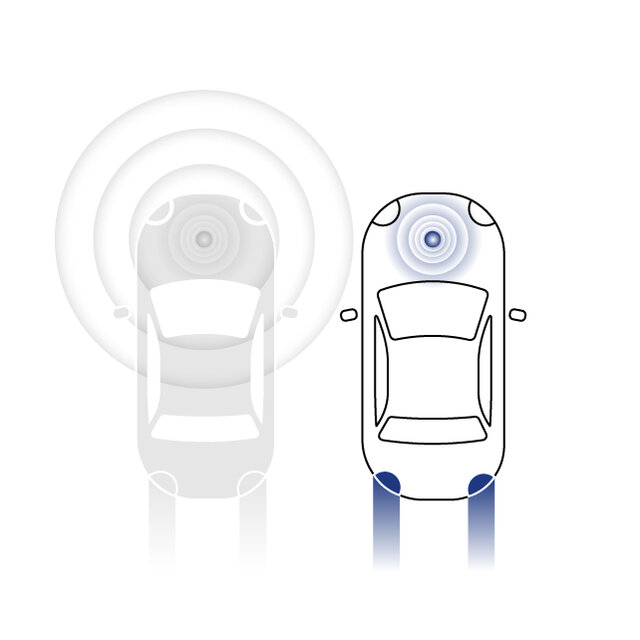
Quality
Significant noise reduction through highest precision.
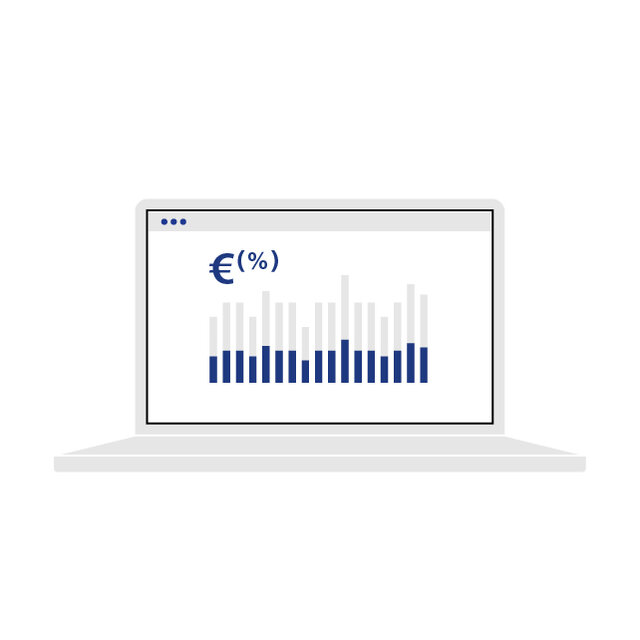
Efficiency
Up to 40 % cost saving with modular complete and combination production.
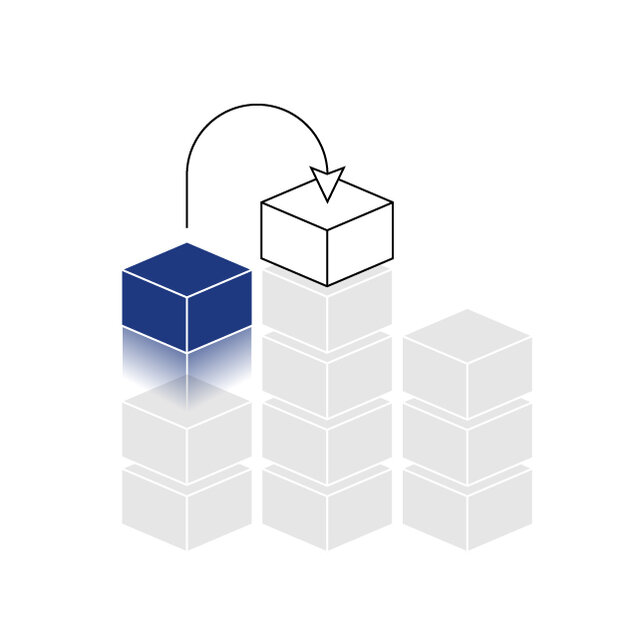
Flexibility
Customisable solutions with synergetic technology systems.
Electric drives place higher requirements on surface and gear quality, as well as on geometric tolerances with their high speeds from 15,000 to 30,000 rpm. WMZ machines for soft machining and Buderus machines for hard fine machining are suitable for complete machining – the number of clamping processes and potential sources of error are significantly reduced.
More important for final product quality are the finely tuned DVS technology systems: Tools, processes and machines within the system are ideally matched, specialists from the individual Group companies are in constant contact with each other and ensure for mutual know-how transfer.
The advantage in quality achieved is not only measurable, it can also be experienced: The significant “Noice Vibration Hardness” (NVH) leads to a noticeably quieter, pleasanter driving experience.
Future-oriented production must also be economically convincing, to be successful in the medium term. The DVS TECHNOLOGY GROUP system solution ensures that the demand on quality does not come into conflict: The modular complete and combination production needs less machines and work steps – and hereby reduces the aquisition and maintanence costs, saves place, energy and personnel. The unit costs sink by 30 to 40 % in comparison with conventional processes – without loss of performance in rotor shaft production.
Whatever the future will bring – one thing is certain: It will bring change. The ability to react quickly and flexibly to changing conditions and demands is a necessary prerequisate for the future viability of a company; it provides the required investment security. The DVS TECHNOLOGY GROUP technology system is constructed modularly. The subcomponents can be adapted or expanded at any time – e.g. with automation. In the case of rotor shafts for electric drives the following components make up the efficient complete solution: The complete production machine from WMZ for complete soft machining of the quill; and, after hardening, the Buderus Schleiftechnik uFlex and 235V machines and the PRÄWEMA Antriebstechnik power-honing machines take over for the hard fine-machining.
The integrated production solution for perfect rotor shafts
Along with the high standards, which electro-mobility requires, the demands are also increased on components, processes and machines. The DVS TECHNOLOGY GROUP responds with modular system solutions and synergetic technology transfer.
Three companies belonging to the DVS TECHNOLOGY GROUP, PITTLER, Buderus Schleiftechnik and PRÄWEMA Antriebstechnik, have bundled their special competences for an integrated production solution for the complete and combination production of monoblock rotor shafts from blank to finished piece. This enables a highly economical production of these sophisticated drive components.
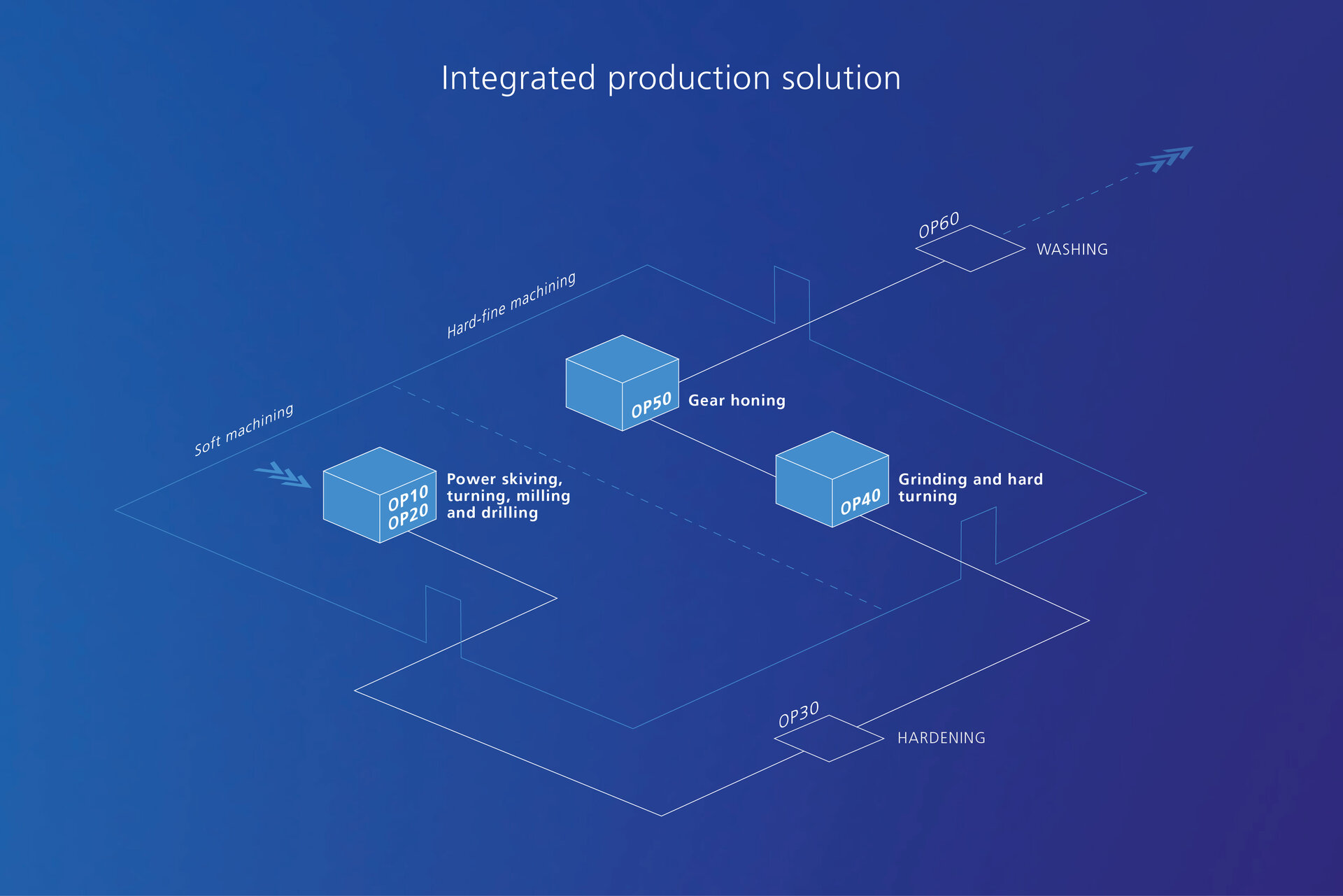
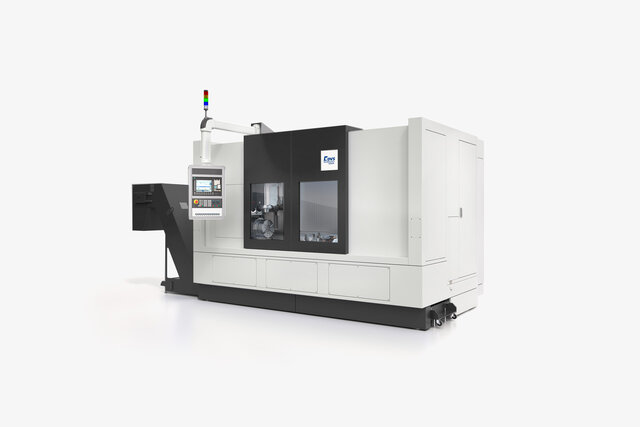
The PITTLER V300‘s carries out the turning, milling, drilling and power-skiving operations in soft machining efficiently and to the highest quality standards with only two clampings.
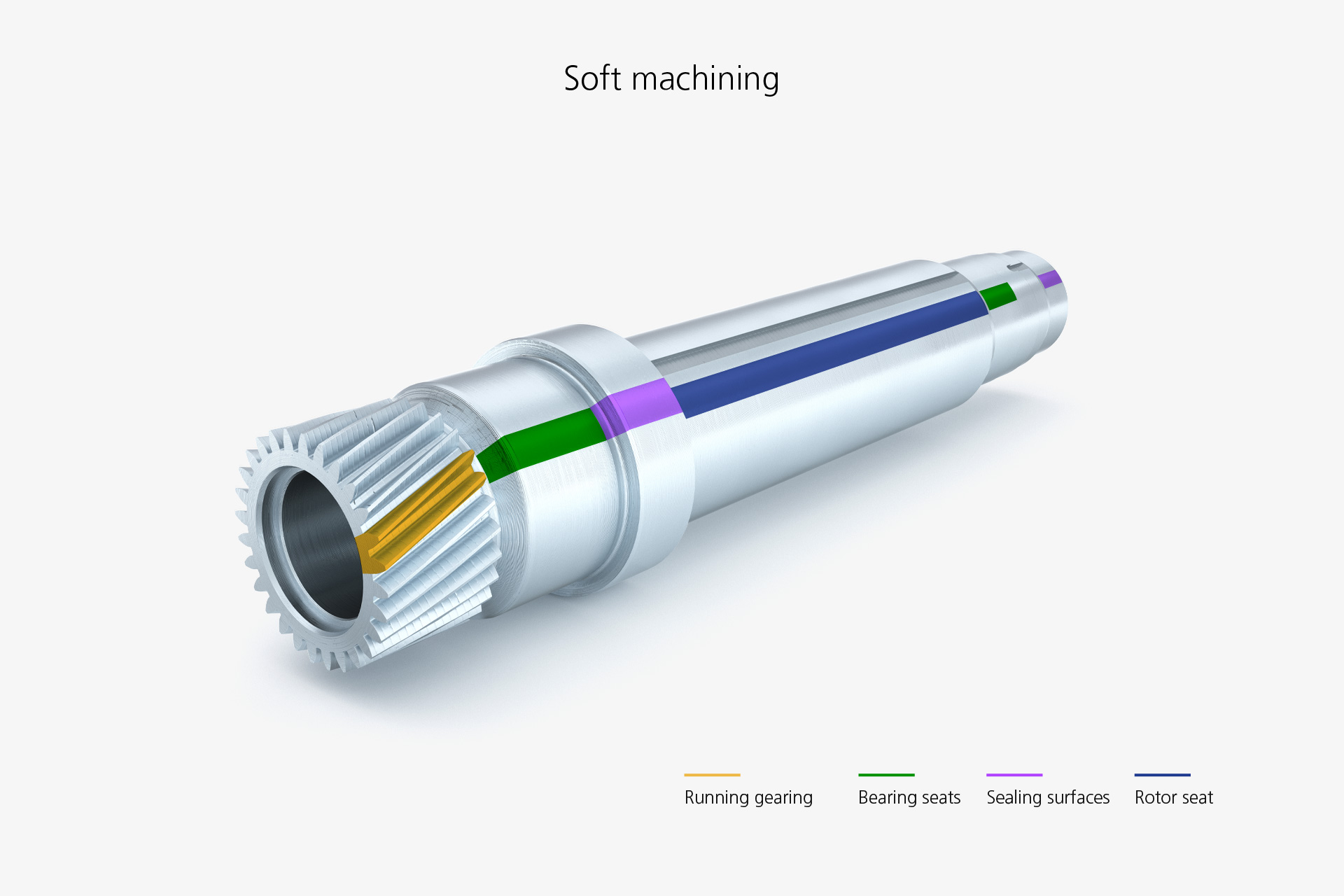
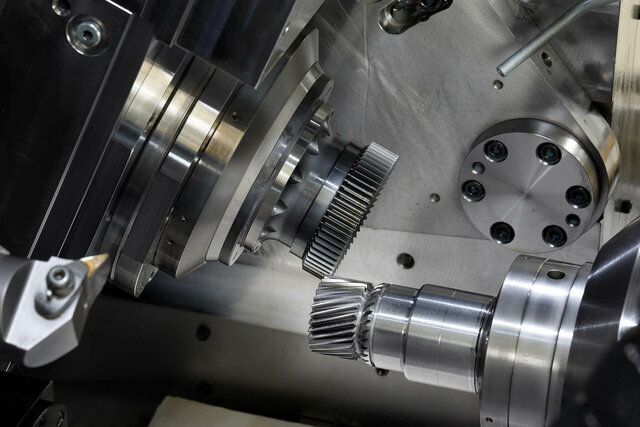
Skiving is a highly precise and very efficient process for the production of running gears and splines.
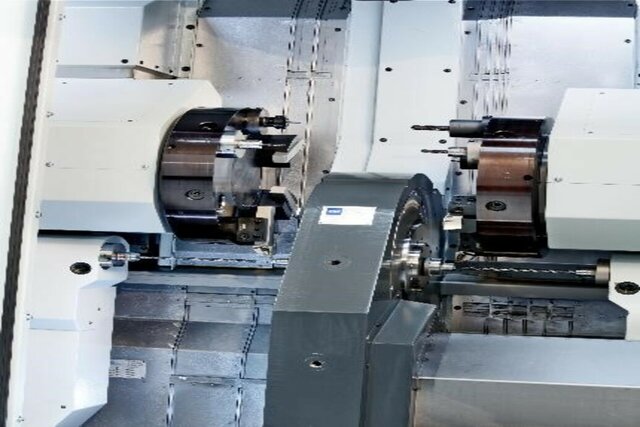
The center drive concept enables machining of the bearing seats and sealing surfaces in a single clamping. The result: very precise runnability.
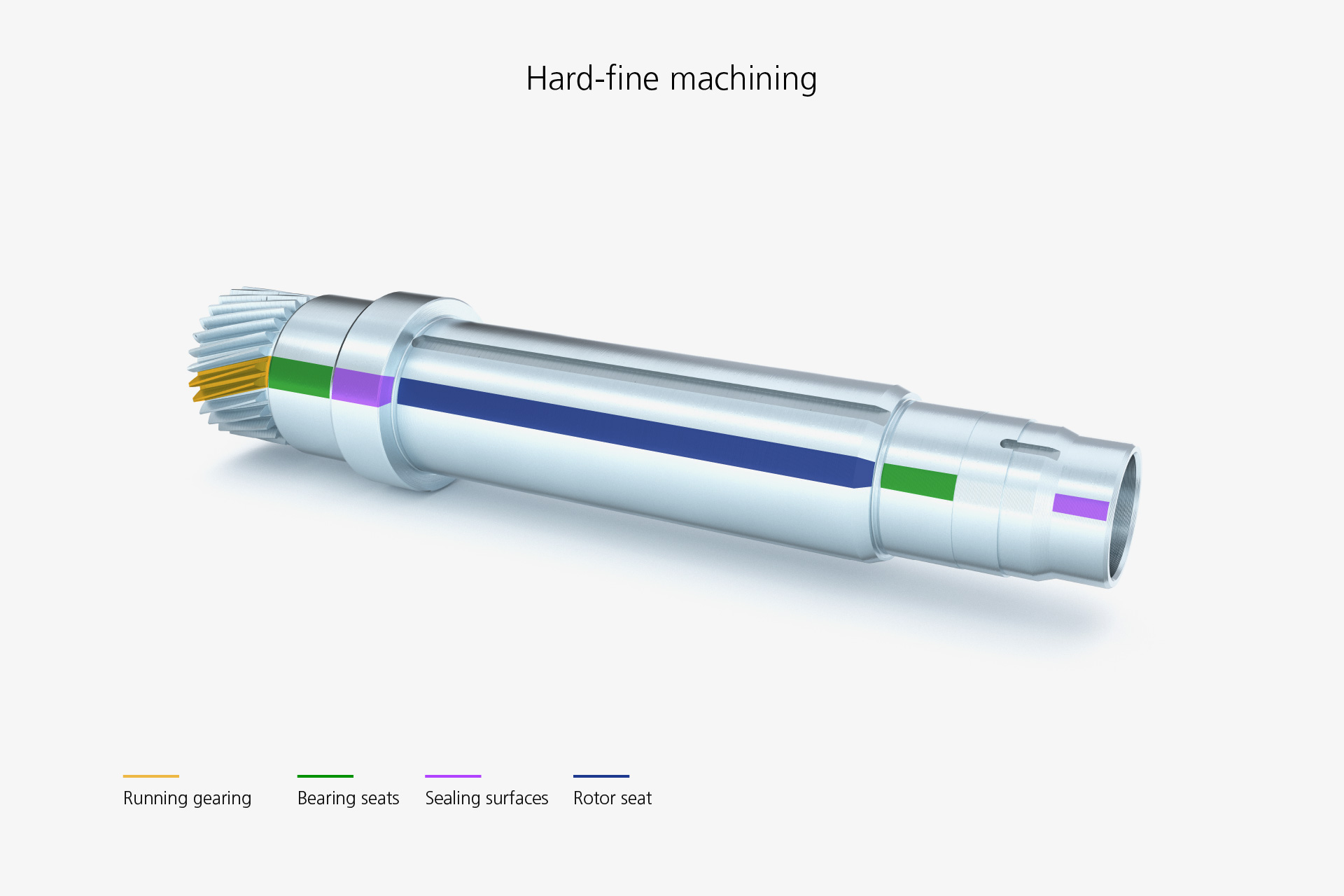
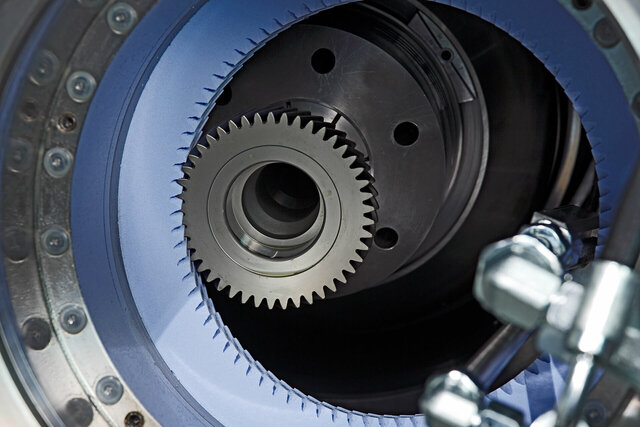
The highly productive process enables ultra-precise machining in gearing qualities IT below 6 and super-fine surfaces with an Rz under 1.
For optimal NVH behavior, specific micro-geometries (e.g., profile angle and profile shape deviations) can be used for the running gears.
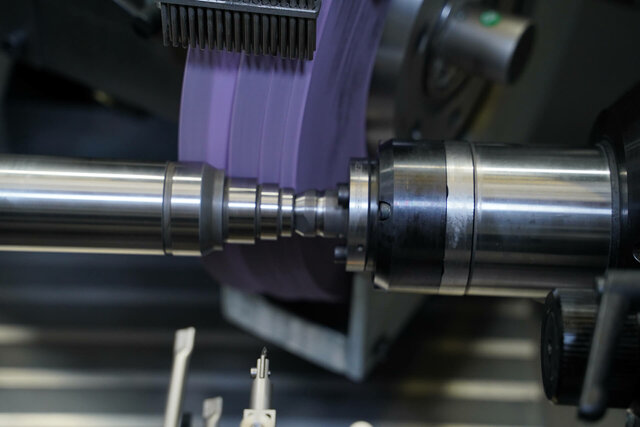
The high speeds of electric drives of up to 30,000 rpm require extremely high accuracies with a wide range of geometric and positional tolerances, e.g., cylindricity of 0.004 mm and coaxiality of 0.005 mm in the bearing seats. The Buderus concept enables ultra-precise machining in the micrometer range in a single clamping while still ensuring high productivity.
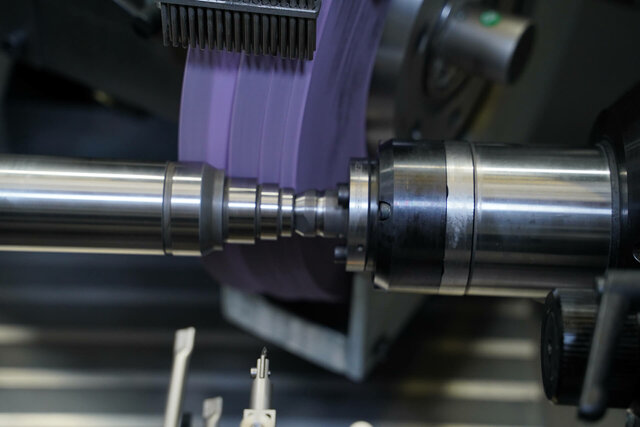
The high speeds of electric drives of up to 30,000 rpm require extremely high accuracies with a wide range of geometric and positional tolerances, e.g., cylindricity of 0.004 mm and coaxiality of 0.005 mm in the bearing seats. The Buderus concept enables ultra-precise machining in the micrometer range in a single clamping while still ensuring high productivity.
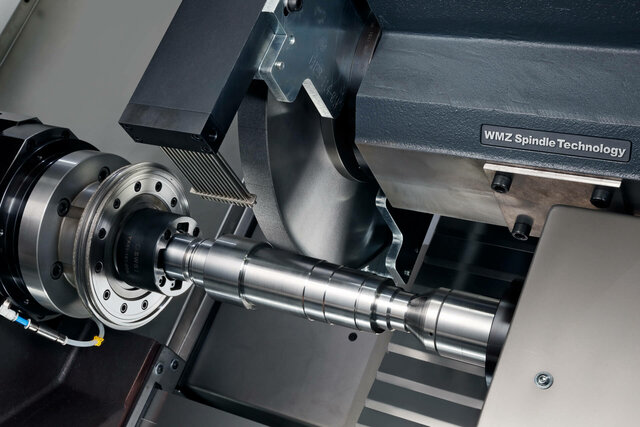
The high speeds of electric drives of up to 30,000 rpm require extremely high accuracies with a wide range of geometric and positional tolerances, e.g., rotor seat roundness of up to 0.002 mm. The Buderus concept enables ultra-precise machining in the micrometer range in a single clamping while still ensuring high productivity.
Case Studies
Electromobility demands the highest quality of individual components - especially in the production of rotor shafts. Our solution for this quality is the perfect interaction of precisely executed machining steps.
Convince yourself what the DVS TECHNOLOGY GROUP's modular technology system can do for you in practical implementation. We will be pleased to send you the related case studies.
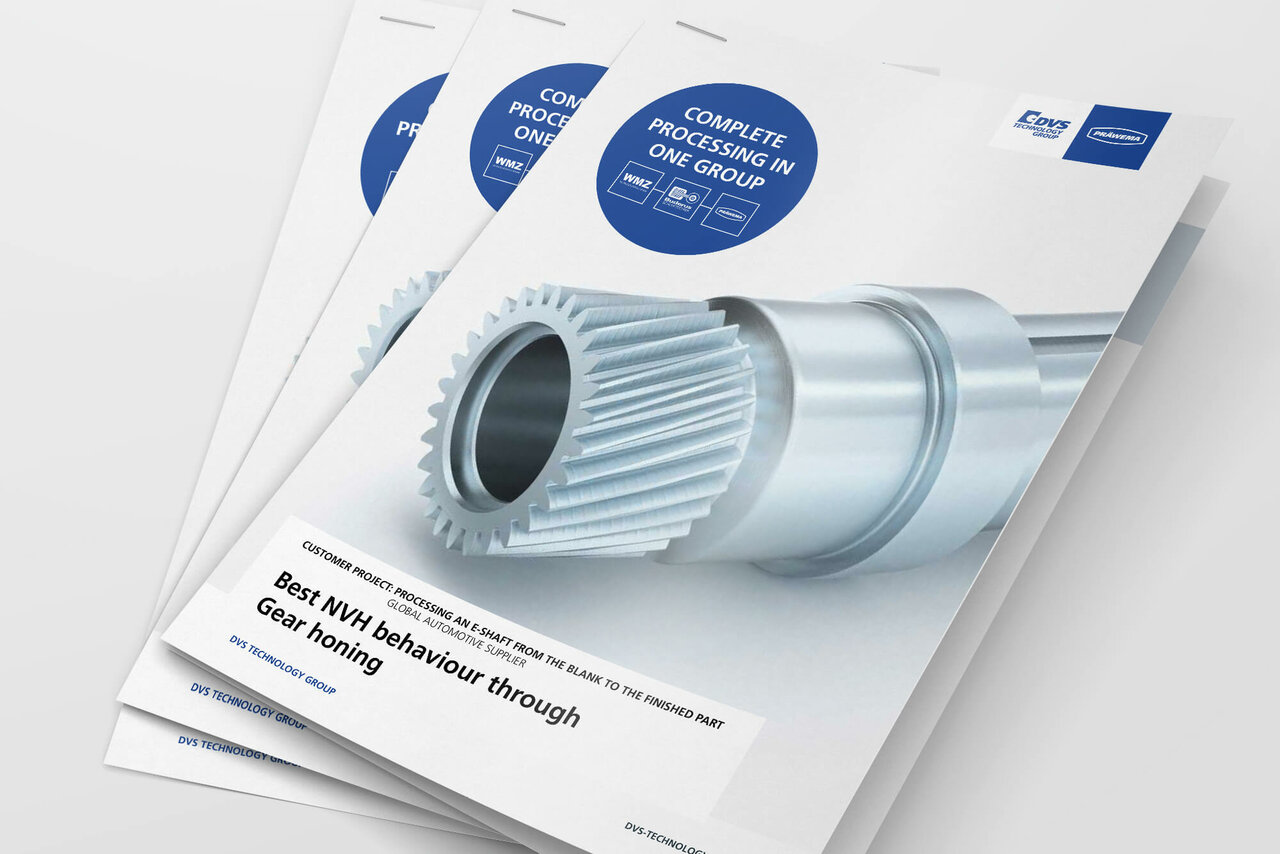
We will be happy to send you examples of application cases for well-known manufacturers and Tier 1 suppliers of electro mobility - simply fill out the answer form!
Do you want to know more about the future of e-mobility?
Talk to our expert about your requirements:
Andreas Prosswimmer
Head of Business Development
T +49 6074 30406 17
E andreas.prosswimmer@dvs-technology.com
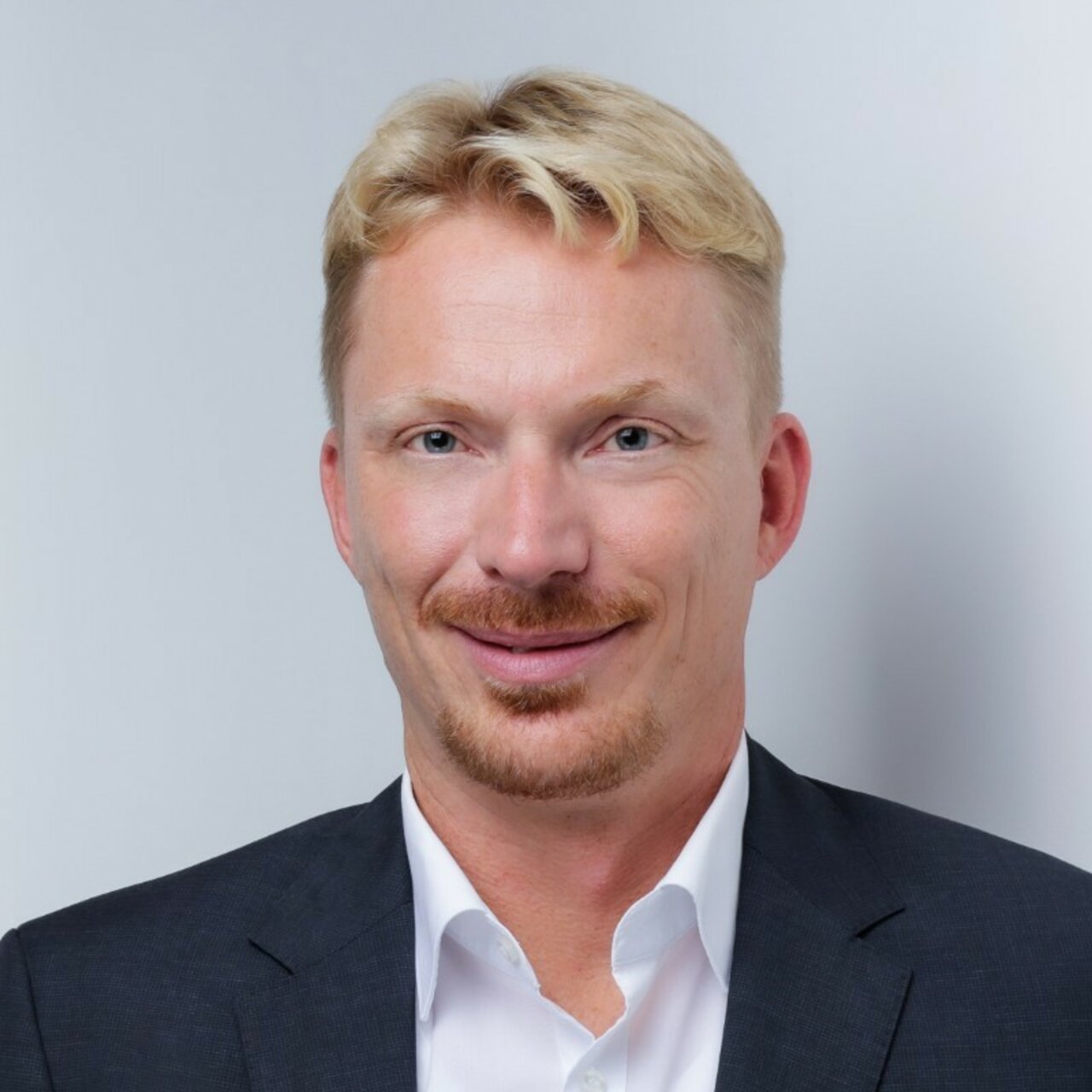