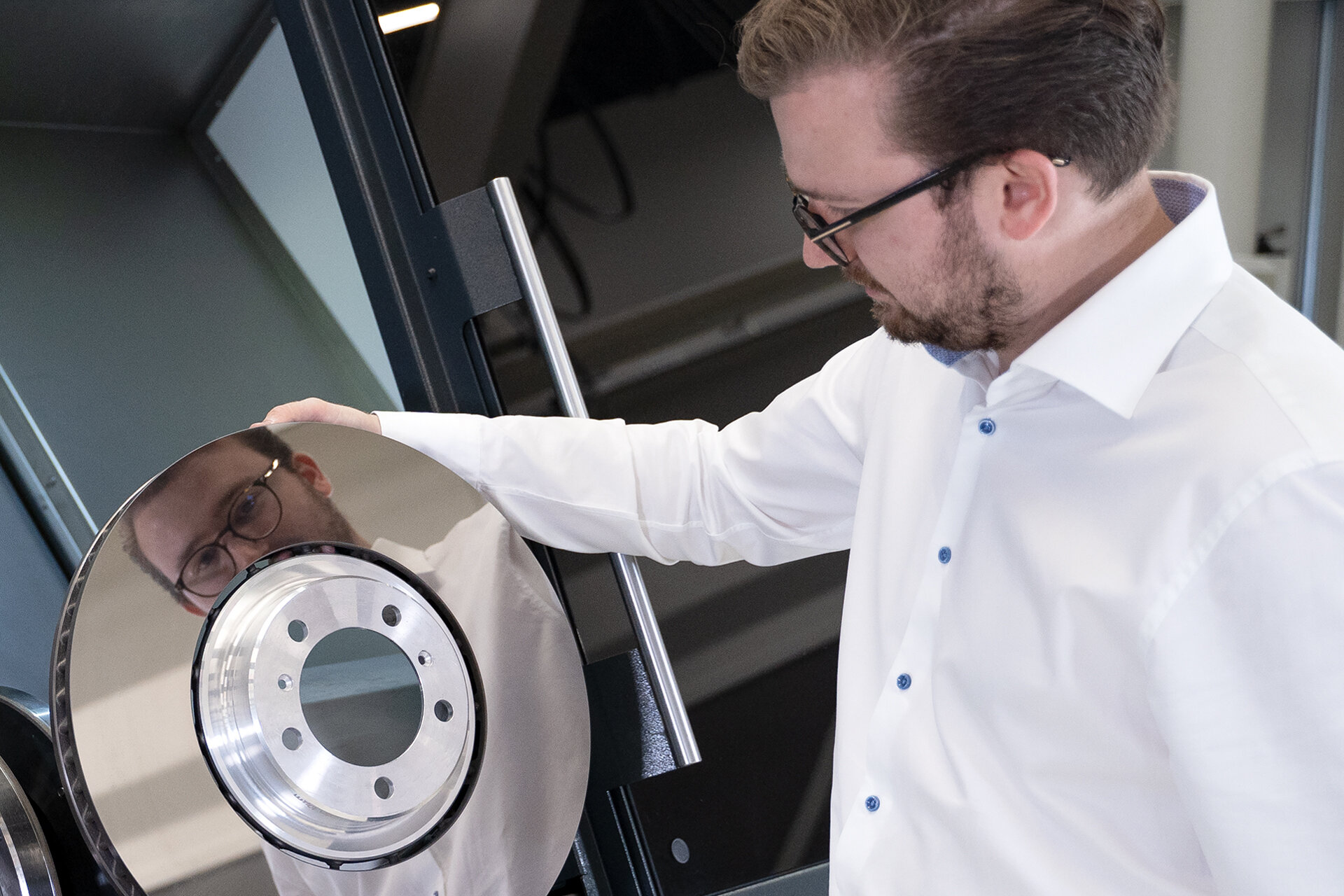
Brake disks for Euro7-compliant brake dust reduction
“Things that benefit drivers and the environment place high demands on production. We have successfully met this challenge.”
Sabri Akdemir
Progress in automotive development has always pushed the limits of what is technically possible. Nowadays, however, additional requirements such as sustainability, safety and efficiency are also becoming increasingly important.
For brake disk production, this means: maximizing performance and service life, minimizing wear and fine dust formation. To produce carbide-coated brake disks precisely and efficiently for this purpose, we have reimagined and modified our proven DVS UGrind.
The result is a new generation of brake disks – made to accelerate progress and to keep pace with the strict regulations of the Euro7 standard.
Environment
High environmental compatibility thanks to 90% less fine dust formation
Safety
More safety through shorter braking distances
Efficiency
Sustainability and efficiency due to extreme durability
A large portion of fine dust emissions in street traffic comes from tire and brake wear. In the future, these emission sources will come into focus under EU7 (European Vehicle Emission Standards). As a technical solution for reducing emissions from brakes, the coated brake disk stands out as the favored response, because it has about 90% fewer emissions than old-fashioned brake disks. In contrast to environmentally stressful brake disks from cast iron, the new coated brake disk is coated with high-strength materials, such as tungsten carbide or titanium carbide, which reduce wear.
Driven to reduce dust by regulations in the Euro7 standard, the current production process for brake disks is massively changing, so that innovative production and process solutions are in demand. For years, DVS TECHNOLOGY GROUP has been successfully participating in these developments by focusing on the grinding process, tools and automation solutions.
The integrated production solution for Euro7-compliant brake disks
Our technologies and solutions
For years, the DVS Technology Group has been a reliable partner to various OEMs and brake disk manufacturers in developing these demanding new workpieces through their expertise and solutions in grinding machine and abrasives technology.
Meanwhile, DVS’s subsidiaries Buderus Schleiftechnik and DVS Universal Grinding have ground thousands of coated brake disks for prototypes and samples. This has brought extremely valuable, important knowledge for further developing the optimal grinding process. Processing brake disks requires series-ready production with high unit counts and fast cycle times.
From planning to implementation, the DVS group of companies offers all the individual technology steps necessary. In addition to machines, the DVS Technology Group also offers abrasives and full automation specially designed for brake disks. This allows our customers to optimize production processes and to strengthen their competitiveness on the brake disk manufacturing market.
Machine types and versions
UGrind800DD |
UGrind1500DDV |
UGrind1500DDS |
Horizontal design |
Vertical design |
Vertical design |
One workpiece spindle, two grinding spindles |
Two workpiece spindles, two grinding spindles |
One workpiece spindle, four grinding spindles |
Compact and economical |
Cycle-neutral loading and unloading possible |
Cycle-neutral loading and unloading possible |
Ideal for large brake disks > 400mm* |
* For workpiece diameters greater than 400 mm, the multifunction head can swivel only without a workpiece.
Do you want to know more about our next-generation brake disks?
Talk to our expert about your requirements:
Andreas Prosswimmer
Head of Business Development
T +49 6074 30406 17
E andreas.prosswimmer@dvs-technology.com
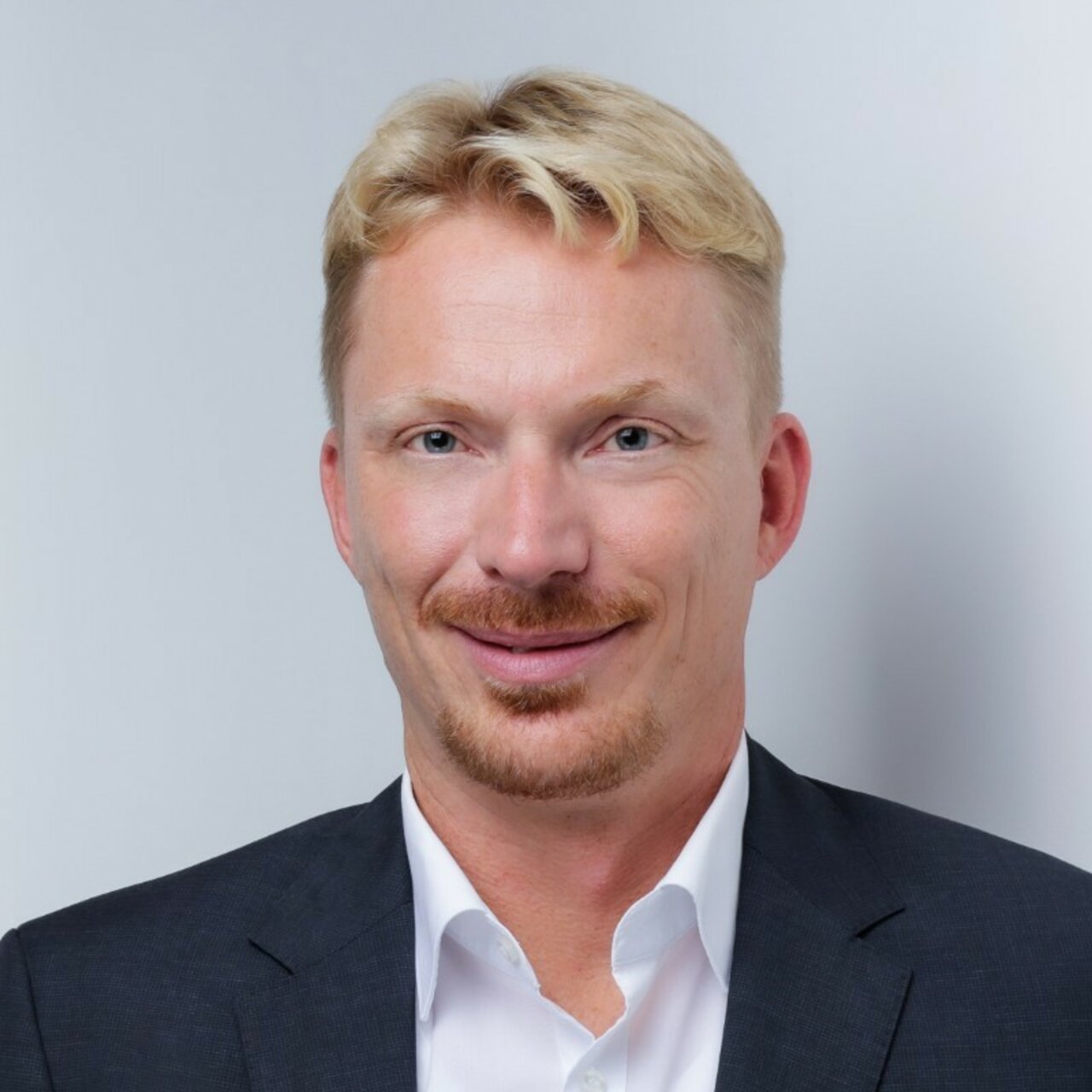