Efficient, precise and flexible - the PITTLER SkiveLine sets new standards in gear production. Thanks to the combination of multifunctional head, Y-axis and automatic tool change, it enables the complete machining of workpieces in a single set-up. This means less set-up time, greater process reliability and a significant increase in productivity.
With its modular design, the SkiveLine adapts perfectly to your production requirements.
- All-in-one machining - skiving, turning, milling, drilling and deburring in just one operation.
- Optimized process times - Automatic tool change for fast and smooth processes.
- Individual automation solutions - Flexible integration of manual loading, swivel loaders or robot systems.
- Space-saving design - Compact design for efficient use of production space.
The PITTLER SkiveLine combines precision, flexibility and cost-effectiveness in an innovative machine solution - for maximum efficiency and quality in modern production.
Highlights
6-axis complete machining: internal and external skiving, turning, milling, drilling, deburring, pointing, backing and measuring in one machine - for maximum efficiency.
Flexible automation options: Choice of crane or manual loading, robot integration or shuttle loading for seamless production.
Fast tool change for reduced non-productive times: 16-position plate magazine ensures automated tool change in just 12 seconds.
Perfect process integration through machine pairing: Direct interaction between two SkiveLine machines enables efficient subsequent processing without additional reclamping.
Maximum precision through machining in a single clamping operation: Reduces reclamping errors and ensures maximum dimensional accuracy in the gearing.
Space-saving and ergonomic design: Compact design with large safety screen for optimum operator protection and easy monitoring of the production process.
Wide range of cooling options for optimum chip removal: emulsion, oil, compressed air or combined systems for extended tool life and improved component quality.
Industry 4.0-ready for smart manufacturing processes: Integrated sensor technology and digital interfaces enable predictive maintenance and efficient production control.
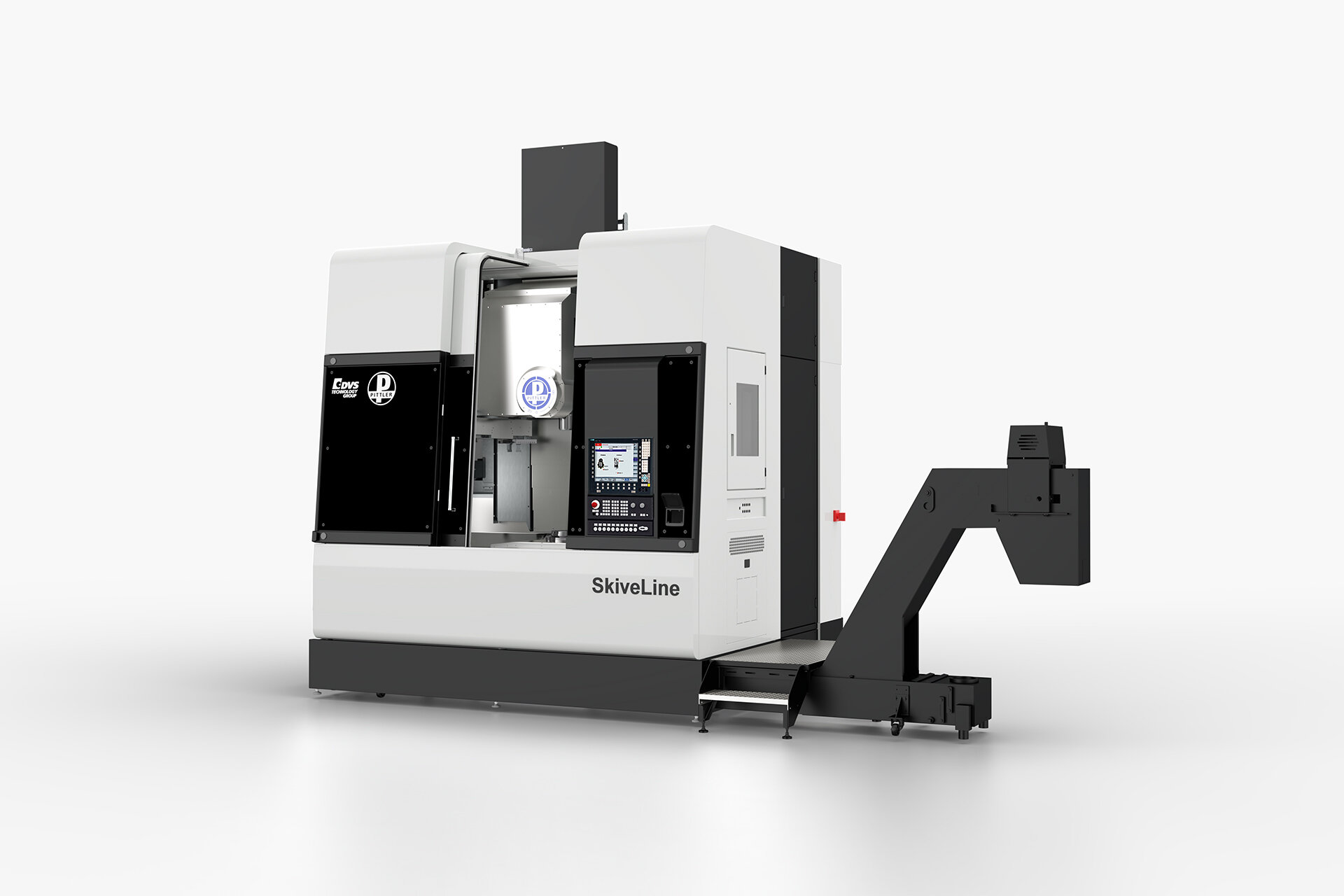
Module: |
SkiveLine PV 315 |
SkiveLine PV 630 |
SkiveLine PV 1250 |
Workpiece diameter max. in mm: |
400 |
630 |
1250 |
Workpiece height max. in mm: |
400 |
400 |
800 |
Technologies: |
6-axis – Complete internal and external machining: turning, milling, drilling, skiving, deburring, measuring, sharpening, backing, impact notching |
6-axis – Complete internal and external machining: turning, milling, drilling, skiving, deburring, measuring, sharpening, backing, impact notching |
6-axis – Complete internal and external machining: turning, milling, drilling, skiving, deburring, measuring, sharpening, backing, impact notching |
Drive: |
Headstock (main spindle C1 and Y-axis), multifunction head (B-axis and C3-axis) |
Headstock (main spindle C1 and Y-axis), multifunction head (B-axis and C3-axis) |
Headstock (main spindle C1 and Y-axis), multifunction head (B-axis and C3-axis) |
Max. S1 – Torque of the main drive [Nm]: |
425 |
1375 |
7440 |
Equipment: |
Compound slide including multifunction head and headstock including Y-axis, tool magazine, swivel loader, automation cell |
Compound slide including multifunction head and headstock including Y-axis, tool magazine, swivel loader, automation cell |
Compound slide including multifunction head and headstock including Y-axis, tool magazine, swivel loader, automation cell |
*Different workpiece geometries require more individual machine designs. For this reason, the technical data given here serve as a guide, but may deviate from reality in individual cases.