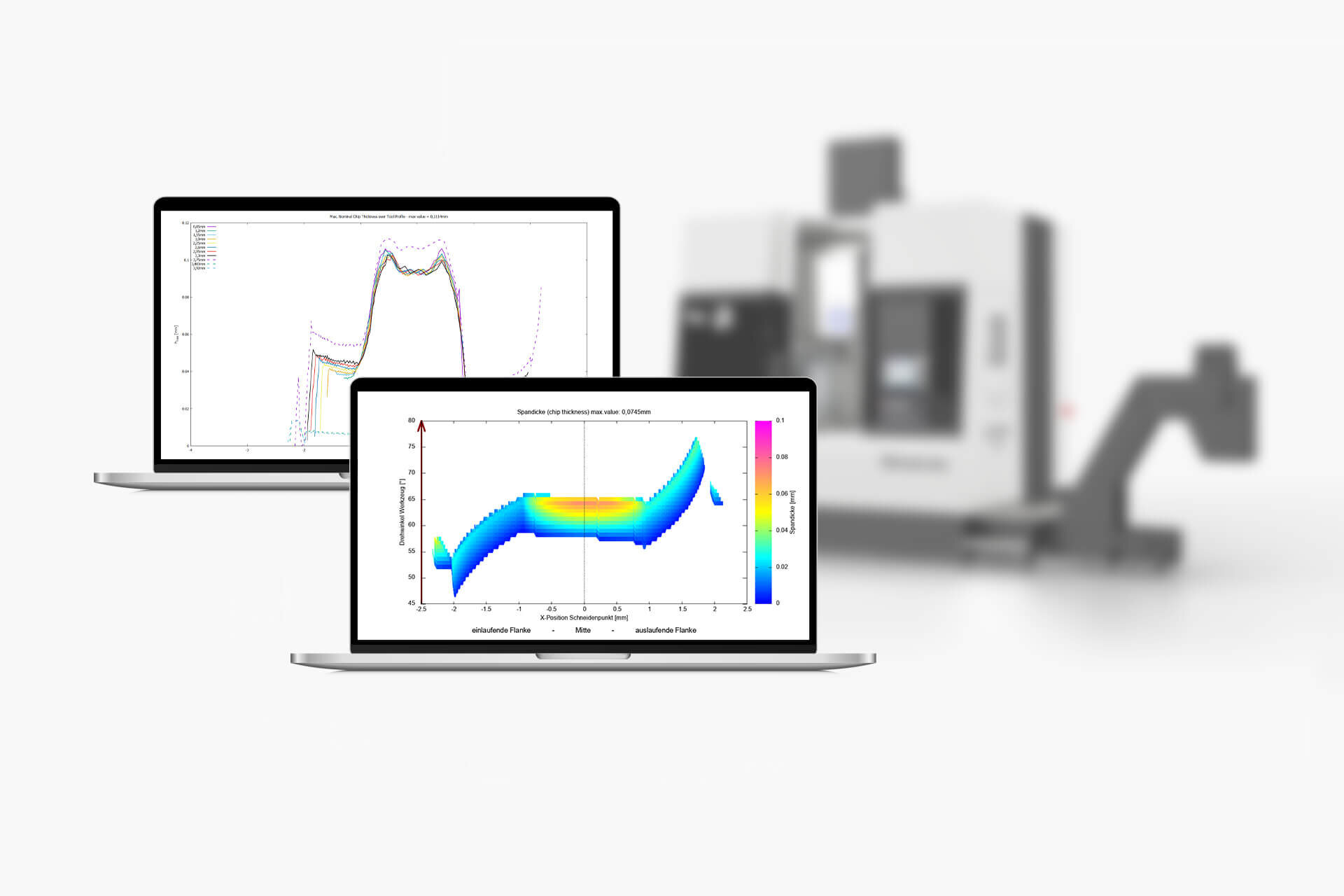
Software solutions in Skiving
PITTLER develops proprietary software solutions in order to meet the growing requirements of our customers and to make the still young manufacturing process of skiving easier to understand. The solutions are designed both for the machine tool and for process analysis on the Windows workstation.
PITTLER SKIVING EXPERT
New workpieces require experienced fitters. PITTLER SKIVING EXPERT offers the perfect solution for an optimal cutting strategy. Depending on the workpiece, tool, and tool material, the software solution suggests a cut allocation with infeed, feed, and speeds in order to quickly achieve short cycle times.
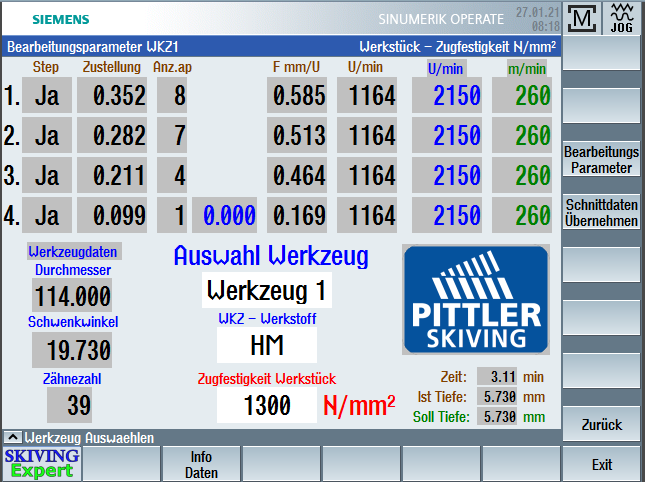
Process analysis with SkivePit
SkivePit gives the engineers and fitters at PITTLER T&S GmbH a better understanding of what is taking place in any given PITTLER SkiveLine machine by providing a wide range of functions, such as the calculation of gearing and tool data as well as the virtual mapping the manufacturing process.
A simulation of the tool's cutting movement shows not only the classic cross-section of the resulting gap, i.e., a horizontal cross-section of the component, but also calculates which areas of the tool cutting edge are actually engaged at which point in time of the cutting movement. This results in the contour of the produced chip.
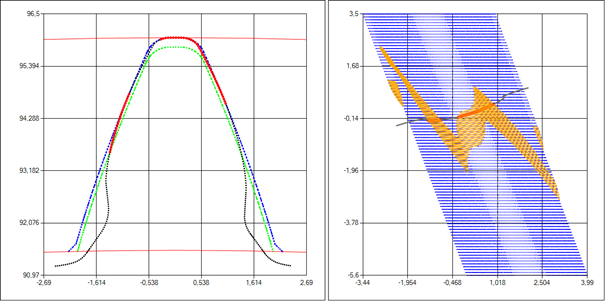
And just like in the actual component, here too it is possible to measure the simulated tooth gap after cutting. SkivePit offers virtual gear measuring to assess the result.
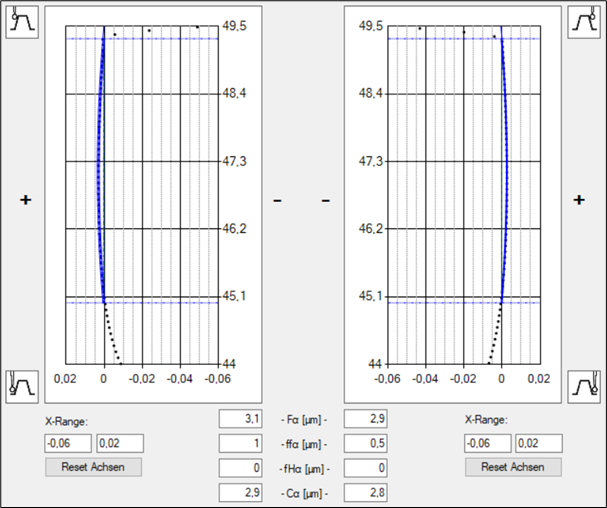
This and many other functions of the company's proprietary SkivePit software enable our engineers to see if your workpieces are suitable for skiving and allow them to offer you suggestions for optimization. We are also offering pre-designed tools with our software.
In the future, the goal is to have a real digital twin and to be able to exchange data directly with the machine tool. This will allow the fitter to test the process virtually in advance, check for any problems, and make the necessary adjustments before the first chip is cut on the machine.
ProAC reduces profile angle errors
ProAC (Profile Angle Correction) reduces profile angle errors during skiving by calculating all relevant machine and workpiece parameters. Since the gear skiving kinematics are always the same in the gear skiving process (and thus also the basis for the calculation), ProAC can be used independently of the machine and on all gear skiving machines.
ProAC uses the principle of approximation (iteration calculation). With this method, variable parameters (e.g., the sigma and kappa angle) are varied according to a specific logic, and the intersection points of the two profile lines are compared with the 0° profile angle error, which enables the calculation of a “theoretical” 0° profile angle error. The limit values that prevent the tool from colliding with the workpiece if the sigma or kappa changes too much are also checked.
ProAC is available online via the DVS Connect Portal or for direct installation on the machine with DVS Edge. For more information, please visit DVS Digital.
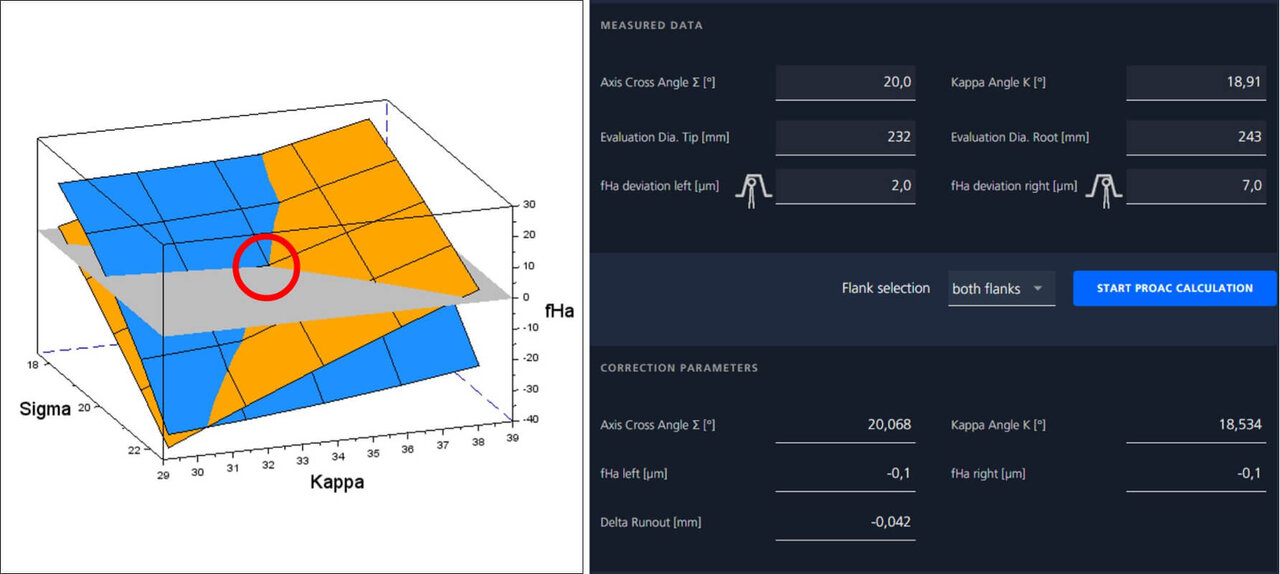