The BV Precision Grinding Machine sets new benchmarks in grinding performance and precision for workpieces with outer diameters up to Ø 4000 mm, enabling efficient grinding with the utmost accuracy. At its core lies a precision-crafted granite base, known for its exceptional thermal stability and rigidity. This fusion ensures outstanding static and dynamic robustness, while minimizing vibrations for exceptional grinding outcomes.
Equipped with two independent processing channels on the cross-slide within the working area, the BV Serie employs play-free roller recirculating linear guides on the step bed for guidance. This arrangement guarantees precise motion control. The X-axis guide rails are directly affixed to the machine bed, ensuring top-notch grinding accuracy. The slide guides are situated above the working area to guarantee optimal safety and results.
The central workpiece spindle, vertically roller-bearing mounted, enables precise workpiece positioning for ultra-precise grinding. Efficiency is maximized as workpieces can be processed in a single clamping.
Die zentrale Werkstücksspindel ist vertikal wälzgelagert und ermöglicht die präzise Positionierung der Werkstücke für hochgenaues Schleifen. Die Effizienz wird maximiert, da Werkstücke in einer Aufspannung bearbeitet werden können.
The first processing channel boasts a dedicated grinding spindle rotary table, carrying a specialized external grinding spindle for precise Curvic gear machining. The second processing channel features a grinding spindle rotary table accommodating both external and internal grinding spindles. The internal grinding spindle is equipped with an HSK 63 mount for swift exchange of grinding arbors and the functional touch probe for exact and pinpoint form and positional tolerance measurements, conducted directly within the machine.
The BV Series comes equipped with an intelligent exchange magazine, integrating both grinding arbors and the measuring unit. This magazine allows fully automated tool changes, substantially boosting productivity. Both cross-slides can be operated independently, facilitating the simultaneous processing of workpieces with specific diameters.
Engineered to meet the highest demands in precision and efficiency, the BV 1000 Grinding Machine features a robust granite machine bed, innovative grinding spindle rotary tables, and an intelligent tool changing system. It presents the optimal solution for demanding grinding tasks. The capacity for simultaneous processing, automated tool changes, and precise measurement techniques render the BV 1000 an indispensable investment for sophisticated manufacturing processes.
As with all machines from BUDERUS Schleiftechnik, the large series also relies on complete machining of the workpieces in a single clamping operation. This eliminates non-productive times for loading and unloading several machines. This is particularly advantageous for large components, where the non-productive times sometimes approach the main times.
However, the biggest advantage of complete machining is the elimination of the reclamping process itself. Since the exact same center is never achieved when the component is reclamped, significantly lower tolerances can be achieved with complete machining, especially when the machined surfaces run in relation to each other.
Thanks to the DVS modular principle, the workspaces of the BV hard machining center can be freely configured to perform as many machining operations as possible in one clamping. Equipped with several cross slides, not only complete but also simultaneous machining is possible.
The cross slides can be moved independently of each other in different directions. This enables the tools to carry out different machining tasks. For example, internal and external cylindrical grinding operations can be carried out simultaneously or combined simultaneously with turning operations. In this way, the machining time can be significantly reduced without compromising the achievable workpiece accuracy.
One to four cross slides run on the hard machining center in backlash-free, high-precision roller guides. These guides consist of a guide rail and the movable slides, which are equipped with roller bearings. This allows high rapid traverse speeds and very small feed movements without a stick slip effect, while maintaining maximum temperature stability without energy-intensive oil cooling. The slides are guided evenly along the entire stroke length in both axes, which means that inherently rigid cutting conditions are achieved across the entire working range.
Processing large components places particular demands on the machine system. The high workpiece weights often make it difficult to handle the components. For this reason, the BV series has a fixed vertical spindle on which the workpieces can be placed relatively easily using lifting equipment.
In addition to gripper systems which, combined with various workpiece conveyors, enable automatic loading of the machine, a two-spindle solution is also available. This allows processing to take place on one side of the machine while the other side is being set up. This virtually eliminates non-productive time for changing workpieces.
For medium-sized and large machines, the spindles are supported axially and radially separately in precision roller bearings. This ensures high concentricity and axial run-out accuracy even with high weights and asymmetrical load distribution.
Overall, the BV is a machine for large workpieces that combines both flexibility and productivity by consistently utilizing the DVS modular principle. This means that the machine can be specially adapted to your application or your range of components. With the large number of possible variants, your machine is sure to be included.
With the “BV Series 500-3000”, we offer you another innovative and reliable technology for the hard fine machining of tomorrow. The development process focused on maximum flexibility, resource-saving production and sustainable management. The compact and modular design enables an individually configurable work area, optimum accessibility and minimal changeover times. The compact design in combination with the very high rigidity offers high-precision, very economical, flexible production.
The unique, sustainable machine bed made of natural granite ensures a high degree of process stability thanks to maximum rigidity, vibration damping, and optimal thermal properties.
Swivel axis (B-axis) under the grinding spindle automatically adjustable with hydraulic locking and "Hirth toothing", swing angle ±90°.
Rotatable dressing spindle enables a wide range of dressing options
Simultaneous machining through configuration with several cross slides
Complete machining in one clamping
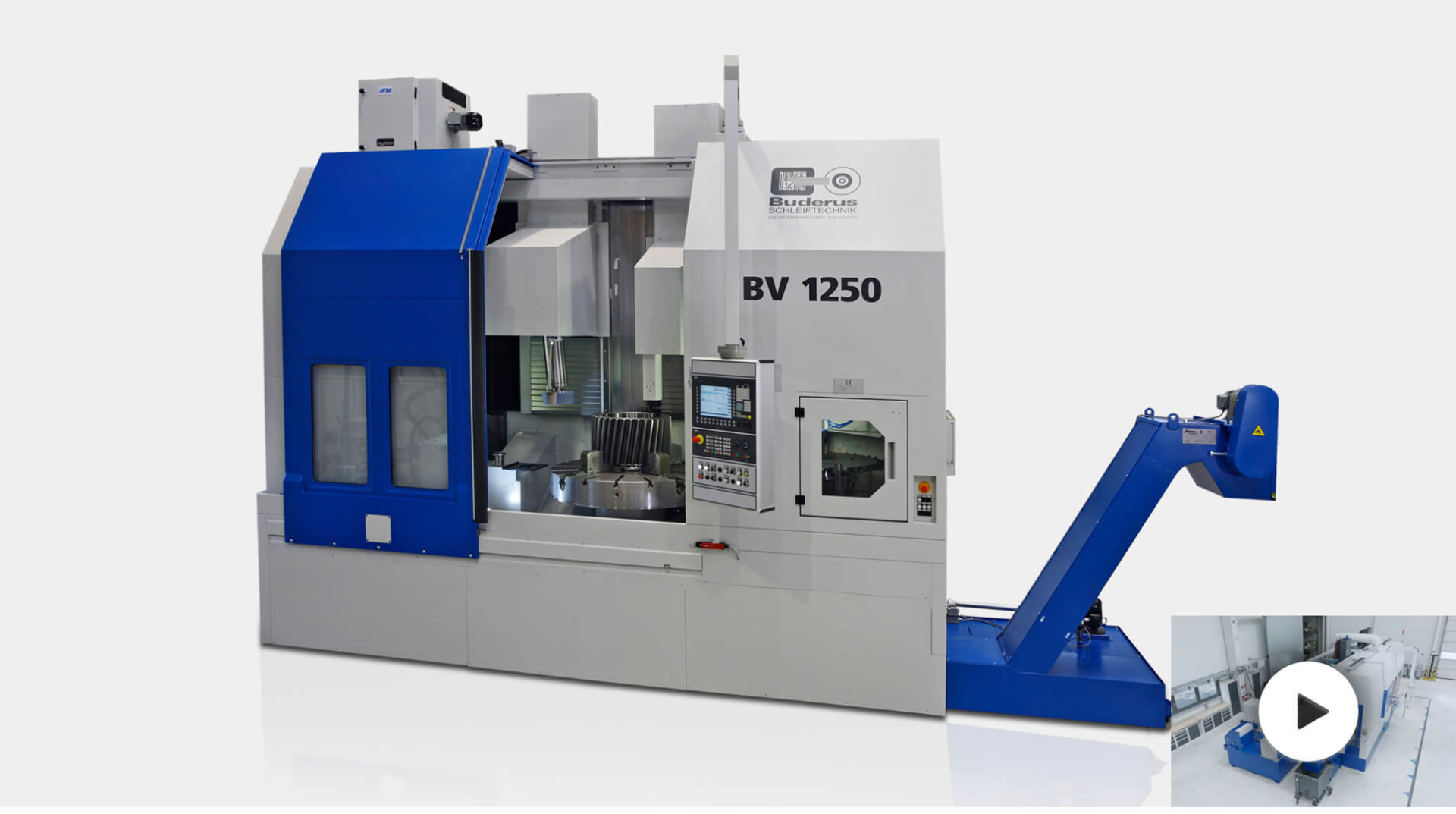
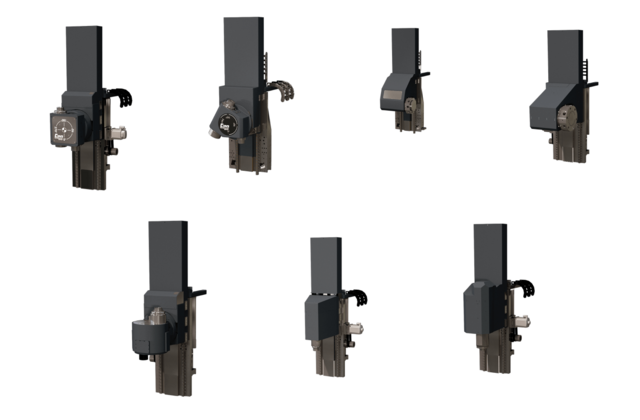
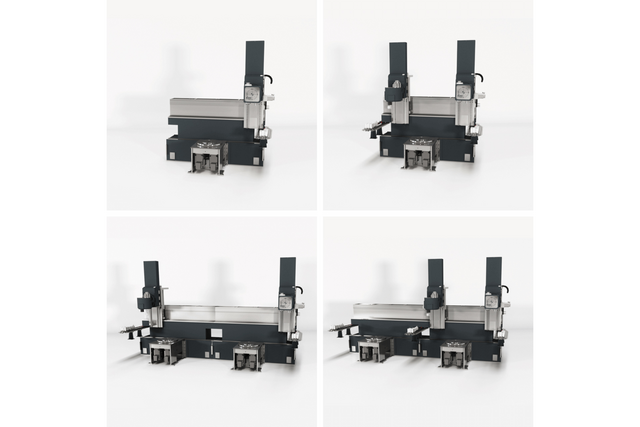
2-axis machining
4-axis machining
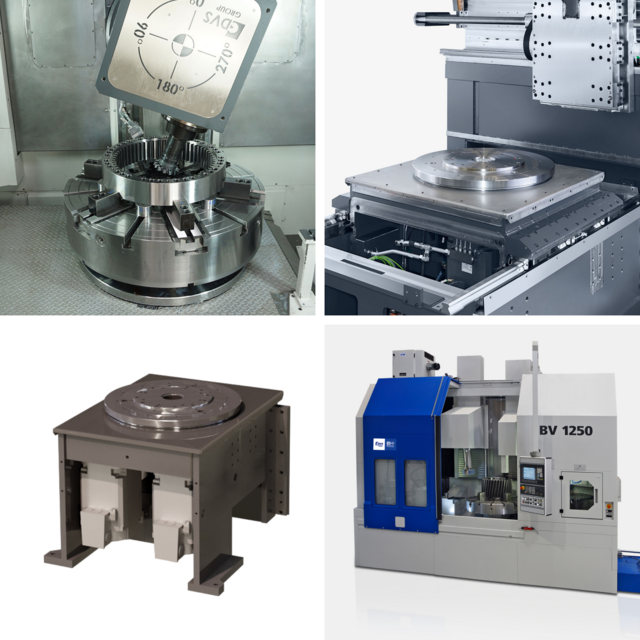
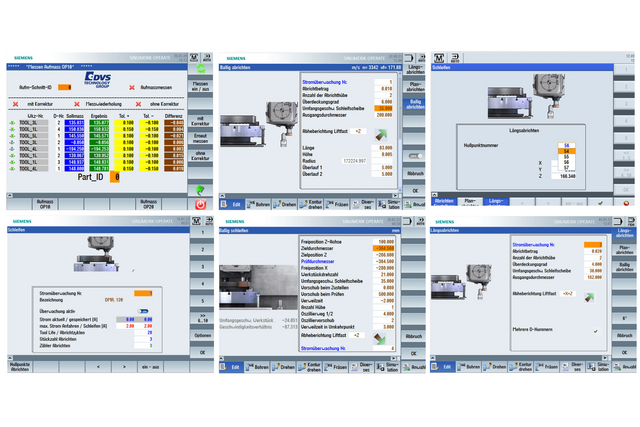
BV 400 |
BV 630 |
BV 800 |
BV 1250 |
BV 1600 |
BV 3000 |
BV 4000 |
|
max. workpiece Ø in mm |
400 |
630 |
800 |
1.250 |
1.600 |
3.000 |
4.000 |
max. workpiece length: |
500 |
500 |
500 |
500 |
500 |
500 |
500 |
max. workpiece weight in kg.: |
500 |
1.500 |
2.500 |
5.000 |
5.000 |
10.000 |
25.000 |
installed power workspindle in kW: |
42 |
78 |
78 |
104 |
104 |
104 |
256 |
No. of workpiece spindles |
1 - 2 |
1 - 2 |
1 - 2 |
1 - 2 |
1 - 2 |
1 |
1 |
max. speed X-axis in m/min |
60 |
60 |
40 |
40 |
40 |
40 |
40 |
max. speed Z-axis in m/min |
30 |
30 |
24 |
24 |
24 |
24 |
24 |
Controller |
Sinumerik 840D |
Sinumerik 840D |
Sinumerik 840D |
Sinumerik 840D |
Sinumerik 840D |
Sinumerik 840D |
Sinumerik 840D |
Footprint basic machine |
4.000 x 2.600 |
4.300 x 2.600 |
4.700 x 2.600 |
5.200 x 3.200 |
5.600 x 3.200 |
6.400 x 3.800 |
9.600 x 7.000 |
Weight in t |
15 |
20 |
25 |
30 |
35 |
40 |
120 |
*Different workpiece geometries require more individual machine designs. For this reason, the technical data given here serve as a guide, but may deviate from reality in individual cases.