No other product is currently as affected by technological change as the automobile and all of its components. Even brake discs are subject to new requirements that must be accommodated by production technology.
Minimizing particulate matter
A significant part of the particulate matter caused by automobiles is due to brake wear, be it from the brake pads or brake discs. Brake discs are produced more wear-resistant, and the friction surfaces are provided with special hard material coatings in order to minimize particulate matter pollution.
Corrosion prevention
While EVs are also fitted with disc brakes, they are rarely used. But their surfaces are exposed to the same weather conditions as those of conventional vehicle brakes. So rust can build up relatively quickly. This is prevented through special coatings that diffuse into the cast. Grinding is subsequently required.
Higher efficiency through lower mass
Brake discs made of carbon ceramic weigh only about 10% of the weight of a cast brake disc and still have better wear and braking characteristics. These types of brake discs can also be processed on the DVS UGrind DD/DDV.
Grinding cast brake discs
Grinding conventional cast brake discs offers a number of advantages over customary lathe machining. Due to the very low wear of the grinding wheels, the tool costs are much lower, while yielding much higher precision and up to 99% contact area on the friction surfaces.
Machining of extremely hard coatings, such as tungsten carbide, aluminum oxide, chromium carbide
Low tool costs thanks to the long service life of DVS grinding wheels
Quick-change chucks for automated operation
Upstream automation and integration into complete production lines possible
Tight tolerances for axial run-out and parallelism as well as high contact area
Greater efficiency and precision when grinding cast brake discs compared to turning
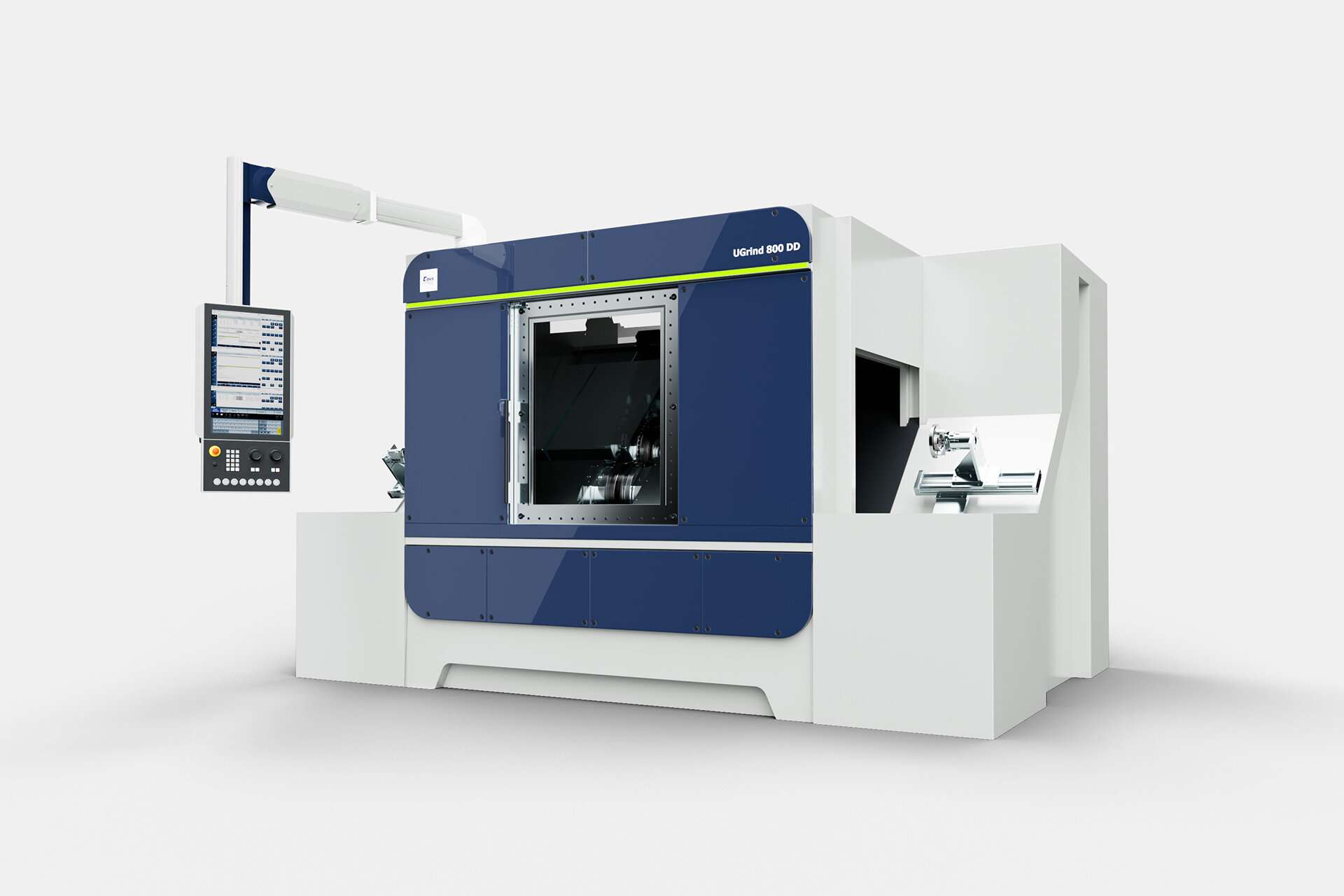
Workpiece diameter min./max. in mm: |
130/500 |
Workpiece thickness max. in mm: |
50 |
Workpiece weight max. in kg: |
40 |
Workpiece spindle speed in rpm: |
0–500 |
Travel distance X in mm: |
250 |
Travel distance Z in mm: |
1200 |
Control: |
Siemens Sinumerik One |
Optional accessories: |
Custom automation solutions, external coolant preparation, chucks, adapted to the relevant brake disc type with bayonet quick-release lock |
Technologies: |
Double-sided surface grinding of brake discs: with hard material coating (e.g., tungsten carbide, chrome carbide, aluminum oxide, silicon carbide) made of carbon ceramic, with corrosion protection coating made of cast iron |
Machine design/structure: |
Sloped machine bed with two grinding spindles that can be moved in the Z-direction, workpiece spindle movable in Z- and X-direction |
Axes/drives: |
Cross slide with X-axis (servo motor + KGT) and Z1-axis (servo motor + KGT) Z2 and Z3 axes (servo motor + KGT), workpiece and tool spindles designed as motor spindles |
*Different workpiece geometries require more individual machine designs. For this reason, the technical data given here serve as a guide, but may deviate from reality in individual cases.