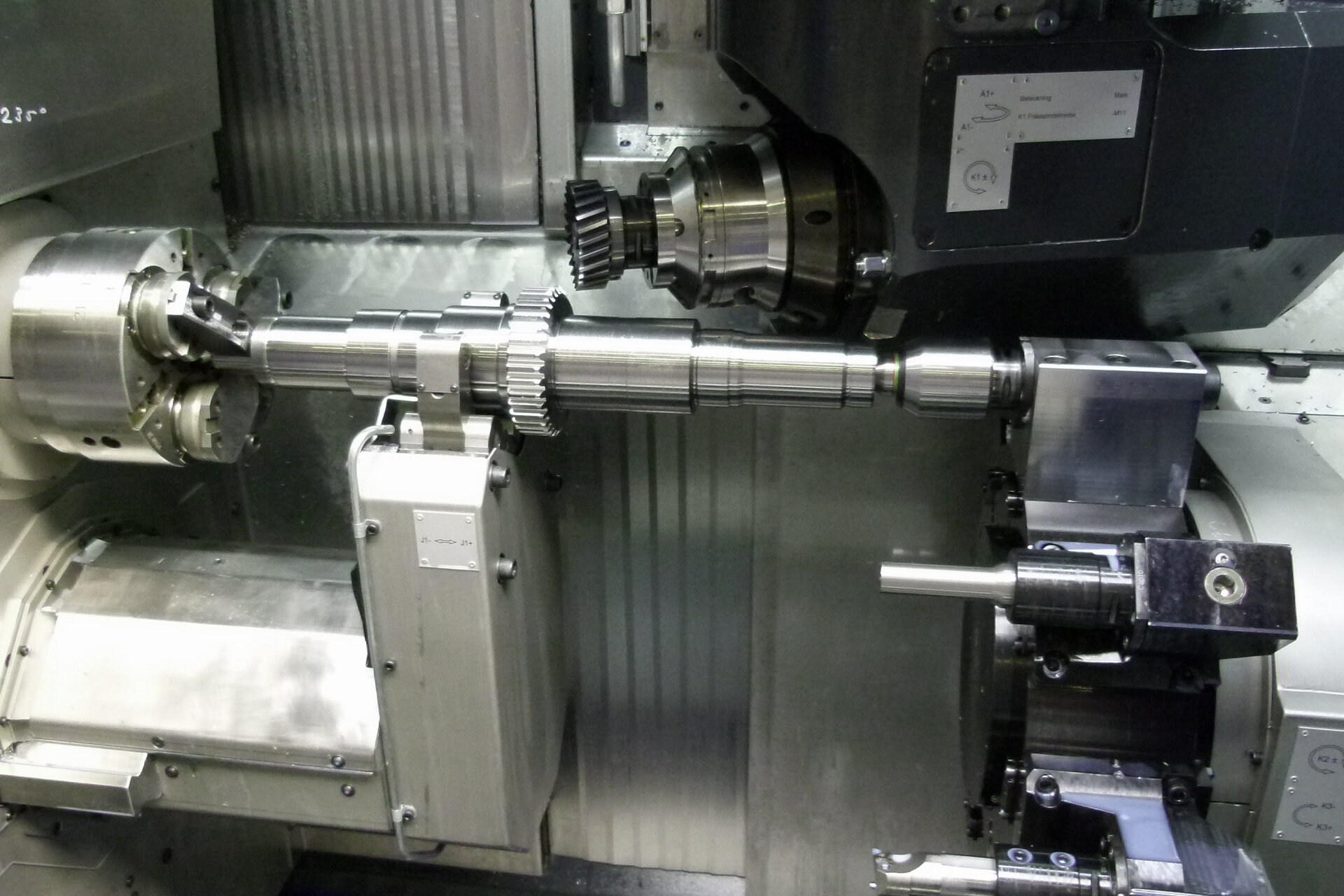
关于什么?
通过多工艺技术完成加工
在WMZ,我们不仅将完整加工理解为车削、铣削、硬车削和磨削的经典组合,而且最重要的是将齿轮切削技术(尤其是滚刀剥离)集成到我们的工艺、机床和系统中。
通过车削、铣削、深孔钻削和滚刀剥离,我们可以对齿轴进行软整理,例如用于汽车或卡车变速器或电驱动。

通过这种方式,我们可以在工件上生产运行和配合齿轮,最高可达模块6,质量高达IT6。
为了不再需要磨削密封表面,我们在机床Y轴的帮助下无扭曲地转动。
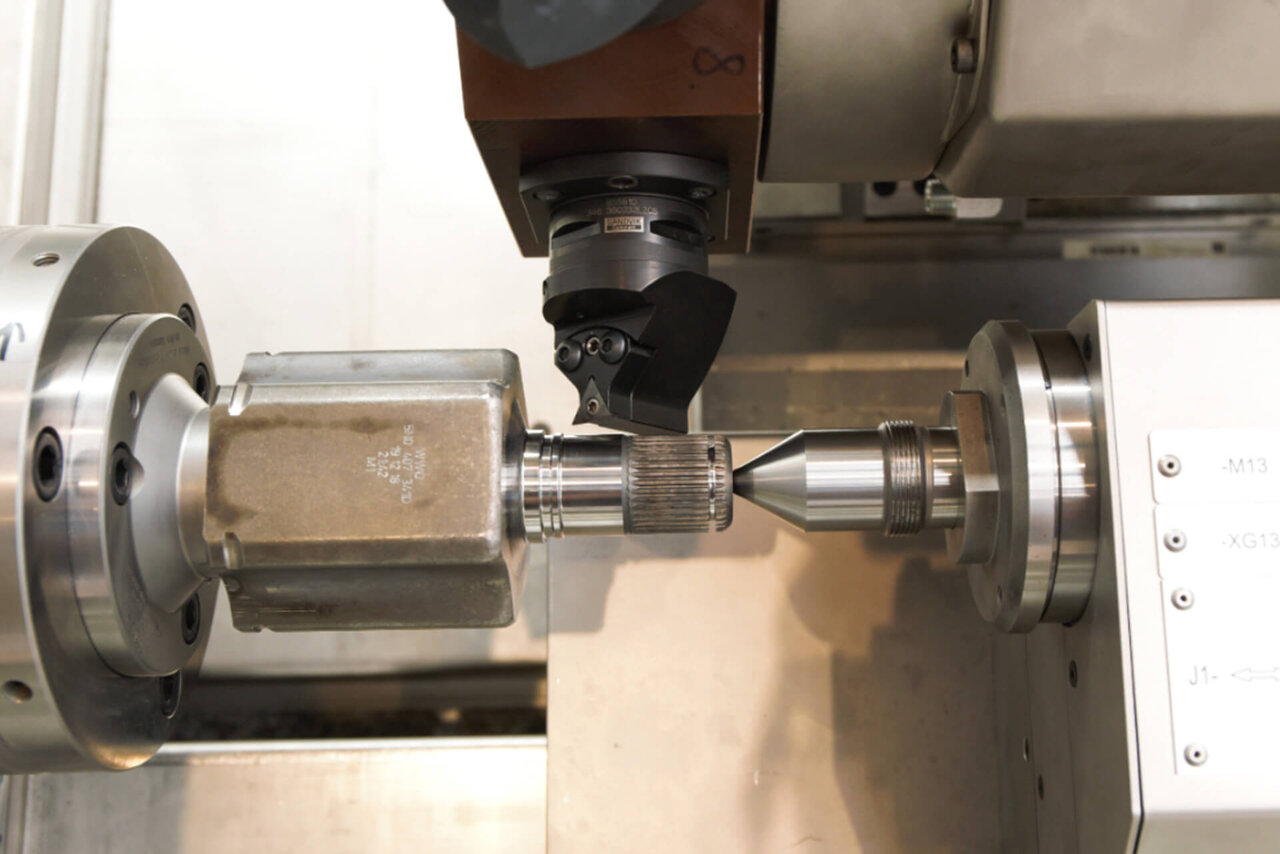
齿轮轴通常具有的通孔或深孔,我们在专门的深孔钻削主轴的帮助下生产。
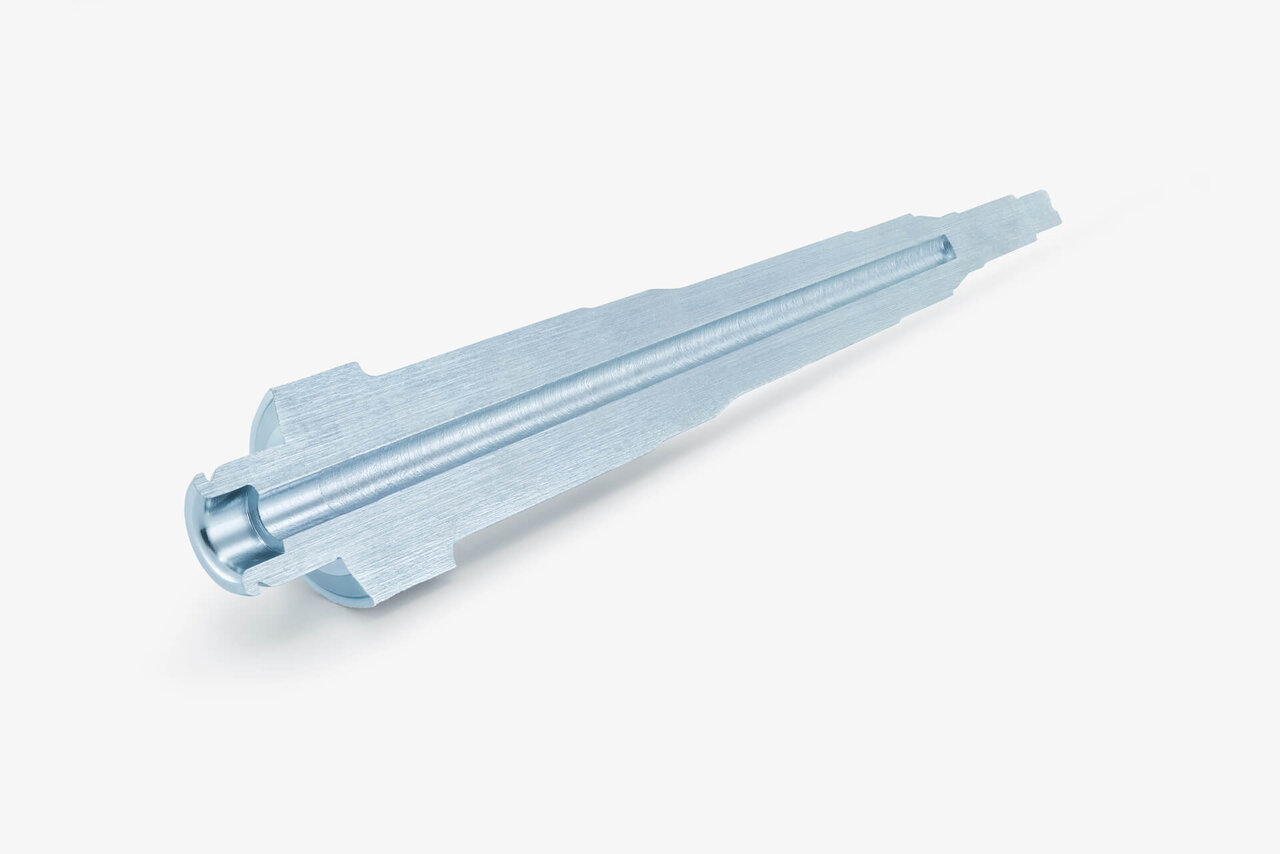
使用深孔钻削主轴,例如,在深孔钻削期间,通过与工件主轴加速增加速度,可以同时加工工件外径。
通过在一次设置中制造轴承座、密封面和齿轮齿,而不需要重新装夹,工件上功能表面的形状和位置公差相互优化。这为工件质量带来了显著的优势,从而也为下游工艺带来了显著的优势。
一种专门适用于滚齿加工一体化的典型机床是WMZ V300,在所示的示例中,卡车变速器的轴在其上进行车削和花键连接。
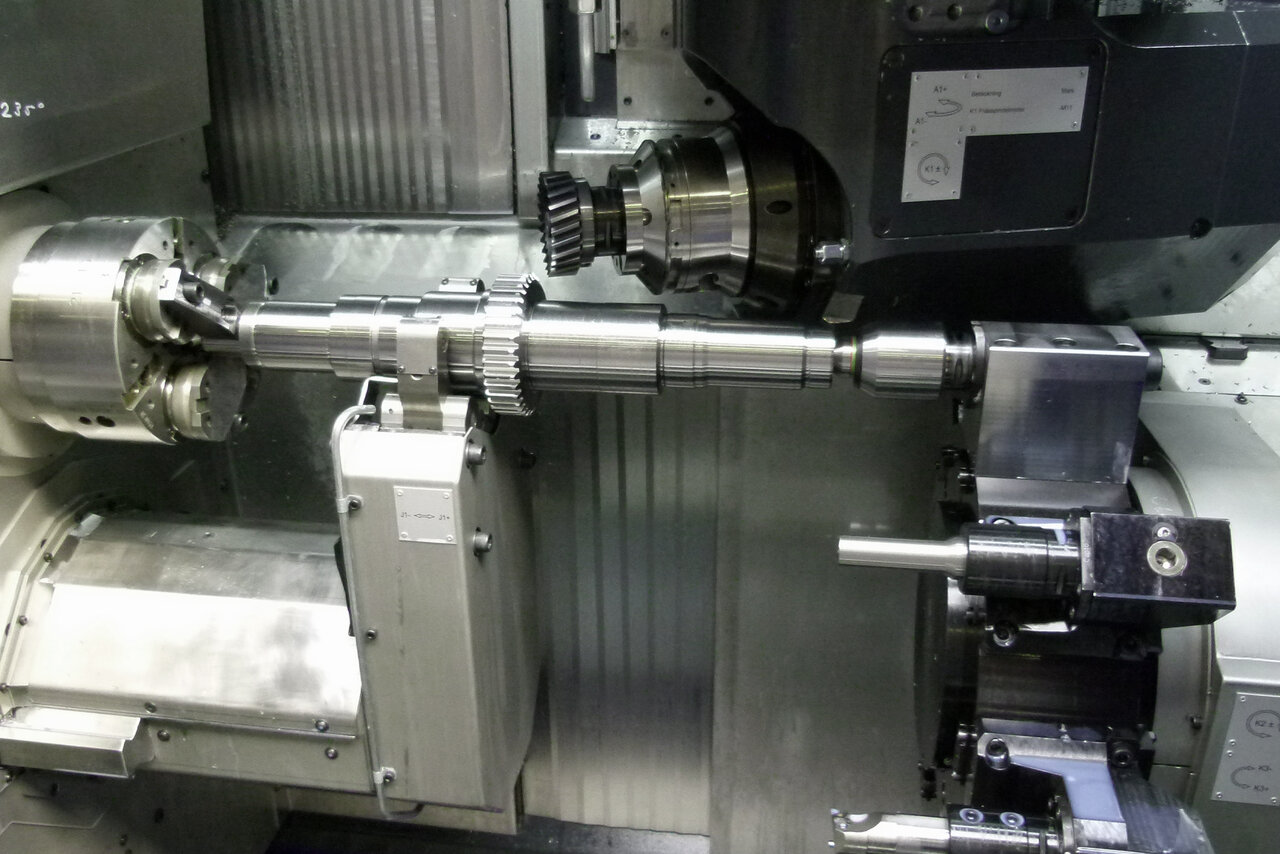
该机床具有一个多功能头,带有刚性安装的铣削主轴。各种铣削或车削刀具可以通过选装的刀库进行更换 - 如有必要,还可以使用补充刀库进行更换。
最重要的是,可以使用不同的滚齿刀具:例如粗加工和精加工刀具,或用于在一个工件上生产具有不同模块的齿轮齿的刀具。
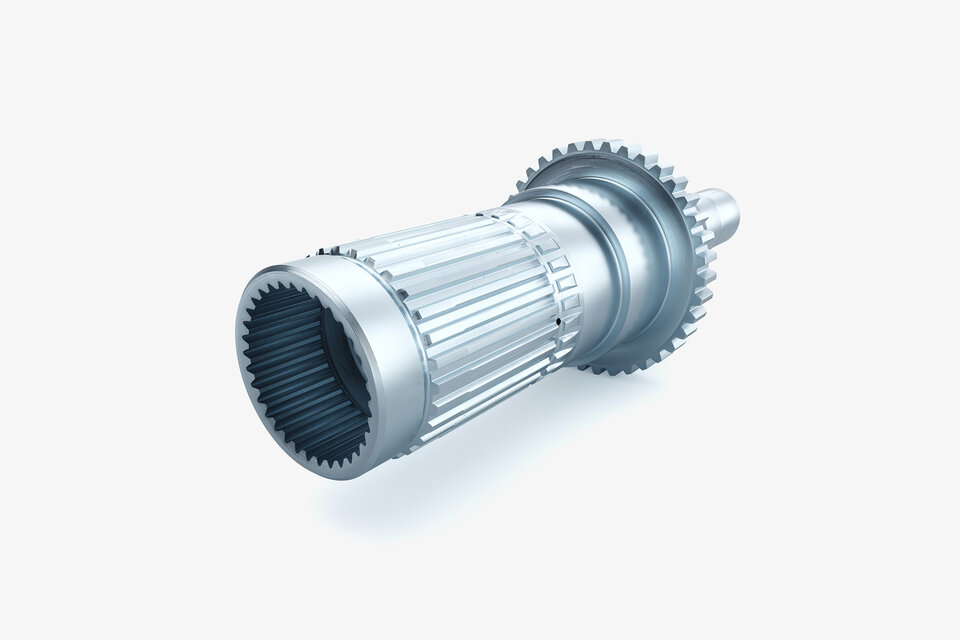
因此,虽然滚齿基本上只能在一台设置机床上生产一组齿(具有多个齿的组合滚刀大大减少了换档范围,增加了刀具磨损和刀具成本),但滚齿更灵活,可以在一个工件上生产不同的齿组。
以DVS内部合同生产电动汽车驱动轴为例,我们明显的可以看到,多技术完整加工不仅在工件质量方面,而且在经济性方面都具有巨大的优势。
在一台WMZ-H200型机床上,我们使用多种技术,在主、副主轴的两种电压下,完整制造了用于两种不同乘用车混合动力驱动的e轴。为此,我们加工中心和内轮廓,钻一个连续的深孔,轧机沟槽和平面,并应用一个运行花键。
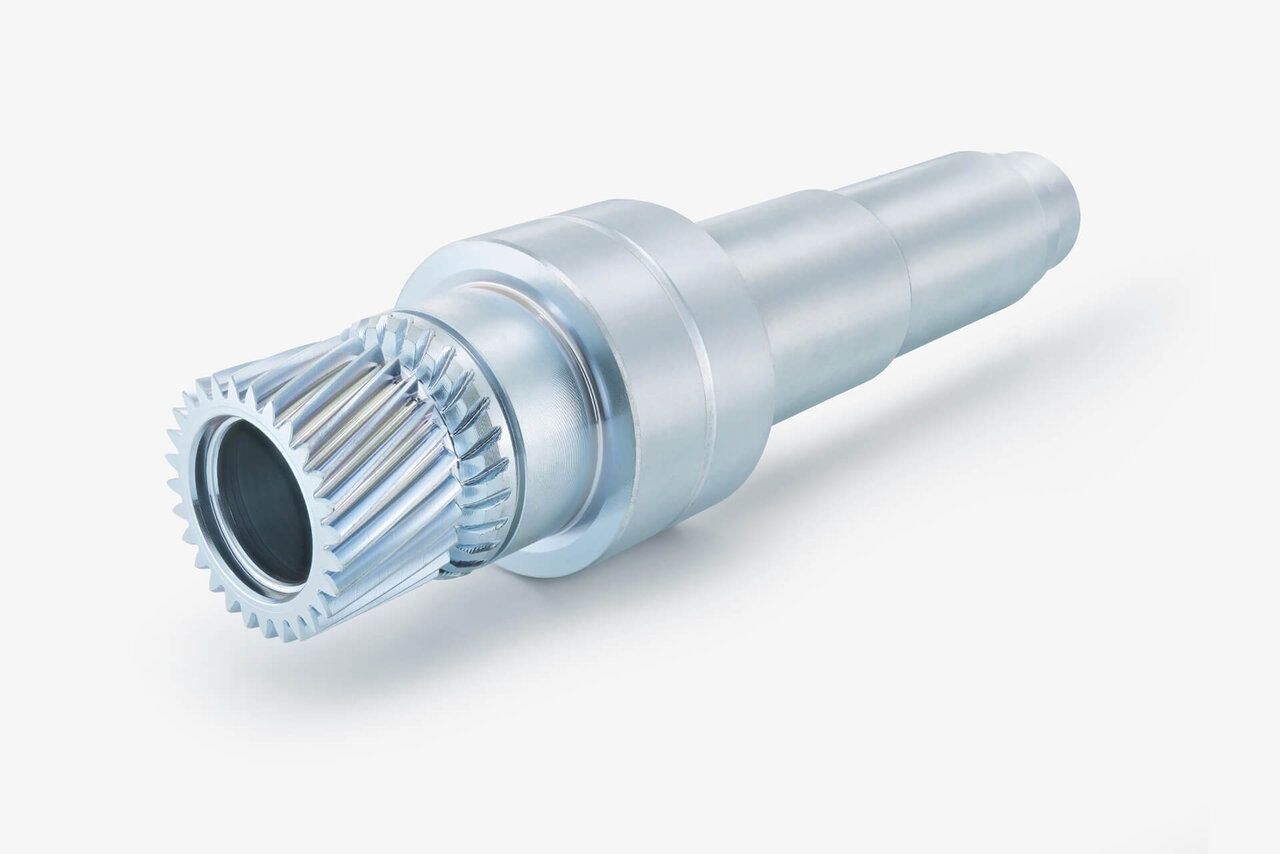
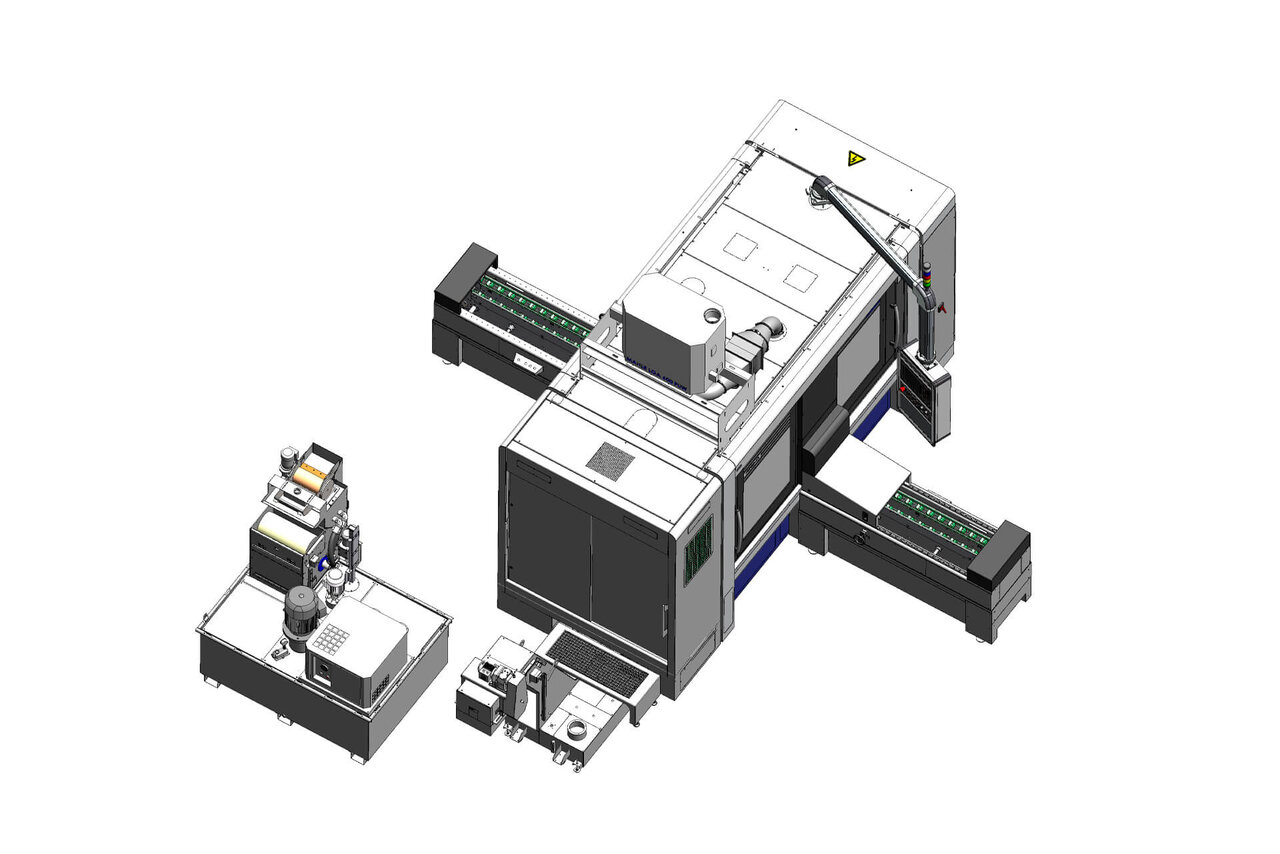
锯切件手动放置在机器的输入输送机上,并通过集成的自动化系统传输到主轴上。工件完全软加工所需的节拍时间为5:50分钟或6:30分钟。这种方法比传统的连接方法有以下优点,例如,四台机器的末端加工,车削外轮廓,深孔钻和齿轮切削:
- 一台机床每年可加工55000 - 65000个完整工件。
- 通过机床数量扩大生产:开始生产机床只需投资一台机床。从一开始就经济地生产不断增长的批量大小,并通过增加更多机床逐步扩大生产能力.
- “呼吸”生产与链条生产线的固定输出进行比较
- 与链条生产线相比,更易于规划和工程设计
- 无需复杂的自动化来连接多台机器
- 多个加工站之间无需内部运
- 更高的输出安全性:在几台机器中的一台发生故障时,与连接线不同,不会出现生产停工。
- 提高预防性维护的可能性,从而提高OEE;机器可以暂时关闭进行维护,而无需停止整个生产。
- 每台机床和班次只需一名操作员,可降低人员成本。
- 总体而言,减少了设置费用。
只需设置一台(复杂)机床
- 轴承座和深孔钻削与齿轮齿完美配合
- 单位成本约为20欧元(这些单位成本远低于在具有4台机床的经典生产线上实现的单位成本,该生产线上也制造了工件)
总之,通过将滚齿集成到轴加工中心中,WMZ创造了一个可扩展的制造解决方案,可以提高工件质量,降低模具成本,提高可用性,最重要的是,最大限度地降低单位成本。