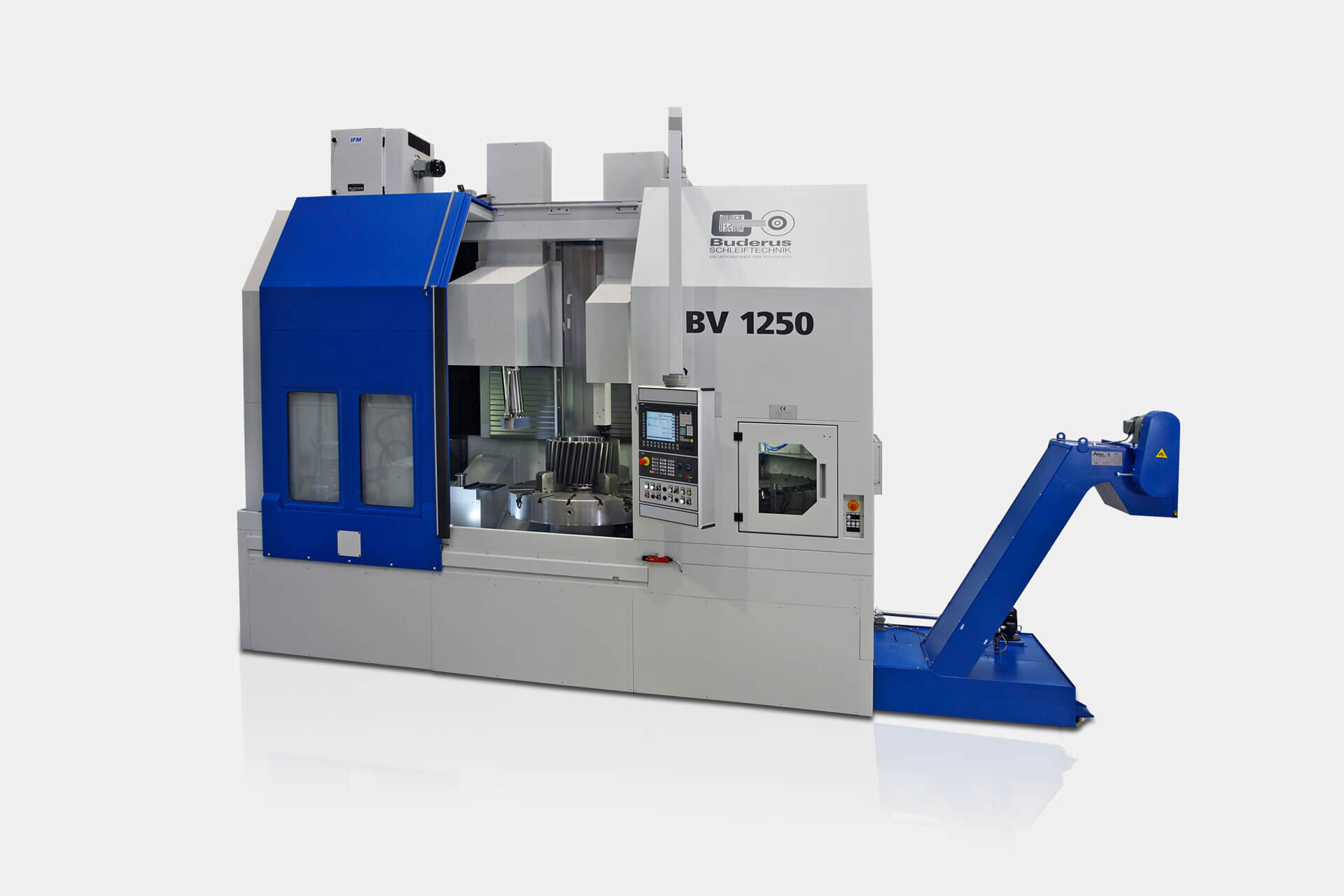
BV 400-4000 – Complete machining in one setup
The BV Precision Grinding Machine sets new benchmarks in grinding performance and precision for workpieces with outer diameters up to Ø 4000 mm, enabling efficient grinding with the utmost accuracy. At its core lies a precision-crafted granite base, known for its exceptional thermal stability and rigidity. This fusion ensures outstanding static and dynamic robustness, while minimizing vibrations for exceptional grinding outcomes.
Equipped with two independent processing channels on the cross-slide within the working area, the BV Serie employs play-free roller recirculating linear guides on the step bed for guidance. This arrangement guarantees precise motion control. The X-axis guide rails are directly affixed to the machine bed, ensuring top-notch grinding accuracy. The slide guides are situated above the working area to guarantee optimal safety and results.
The central workpiece spindle, vertically roller-bearing mounted, enables precise workpiece positioning for ultra-precise grinding. Efficiency is maximized as workpieces can be processed in a single clamping.
Die zentrale Werkstücksspindel ist vertikal wälzgelagert und ermöglicht die präzise Positionierung der Werkstücke für hochgenaues Schleifen. Die Effizienz wird maximiert, da Werkstücke in einer Aufspannung bearbeitet werden können.
The first processing channel boasts a dedicated grinding spindle rotary table, carrying a specialized external grinding spindle for precise Curvic gear machining. The second processing channel features a grinding spindle rotary table accommodating both external and internal grinding spindles. The internal grinding spindle is equipped with an HSK 63 mount for swift exchange of grinding arbors and the functional touch probe for exact and pinpoint form and positional tolerance measurements, conducted directly within the machine.
The BV Series comes equipped with an intelligent exchange magazine, integrating both grinding arbors and the measuring unit. This magazine allows fully automated tool changes, substantially boosting productivity. Both cross-slides can be operated independently, facilitating the simultaneous processing of workpieces with specific diameters.
Engineered to meet the highest demands in precision and efficiency, the BV 1000 Grinding Machine features a robust granite machine bed, innovative grinding spindle rotary tables, and an intelligent tool changing system. It presents the optimal solution for demanding grinding tasks. The capacity for simultaneous processing, automated tool changes, and precise measurement techniques render the BV 1000 an indispensable investment for sophisticated manufacturing processes.
The unique, sustainable machine bed made of natural granite ensures a high degree of process stability thanks to maximum rigidity, vibration damping, and optimal thermal properties.
Swivel axis (B-axis) under the grinding spindle automatically adjustable with hydraulic locking and "Hirth toothing", swing angle ±90°.
Rotatable dressing spindle enables a wide range of dressing options
Simultaneous machining through configuration with several cross slides
Complete machining in one clamping
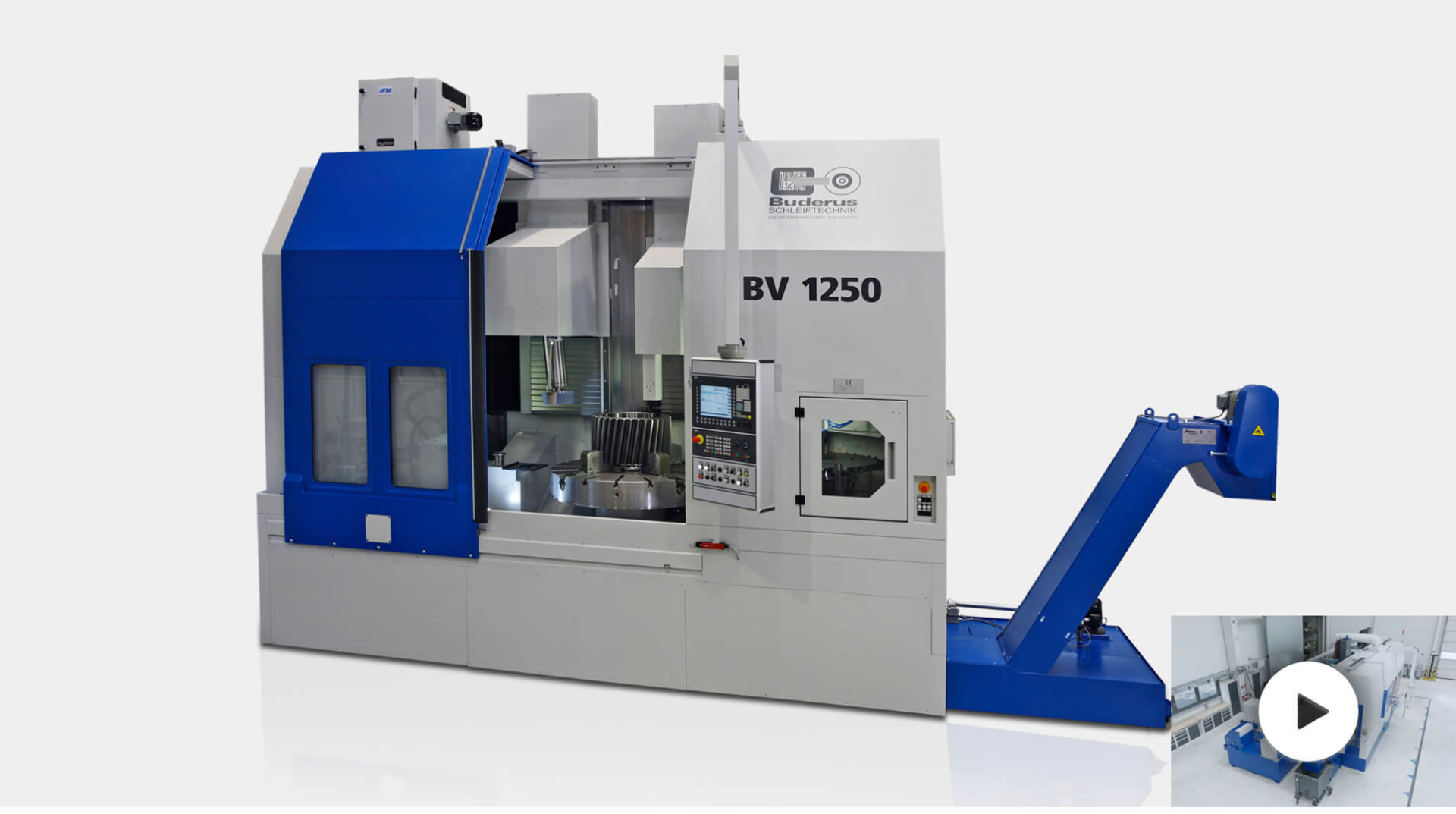
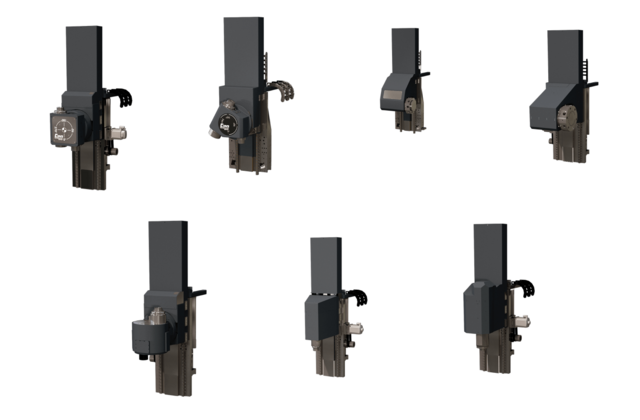

2-axis machining
4-axis machining
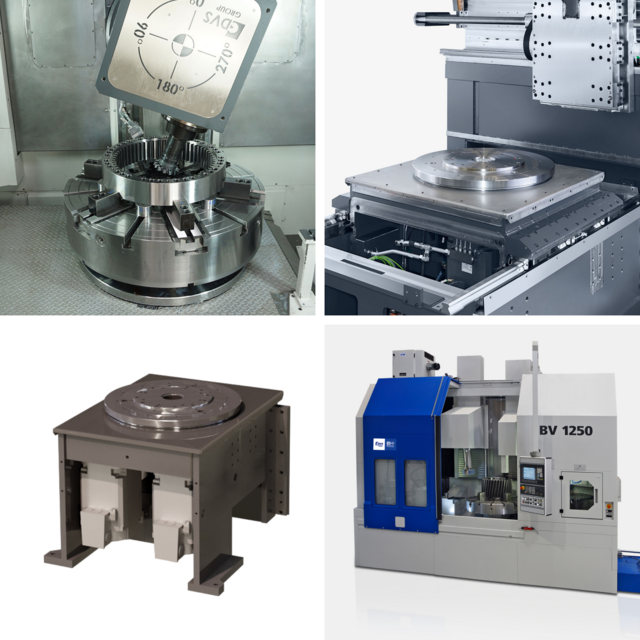

BV 400 |
BV 630 |
BV 800 |
BV 1250 |
BV 1600 |
BV 3000 |
BV 4000 |
|
max. workpiece Ø in mm |
400 |
630 |
800 |
1.250 |
1.600 |
3.000 |
4.000 |
max. workpiece length: |
500 |
500 |
500 |
500 |
500 |
500 |
500 |
max. workpiece weight in kg.: |
500 |
1.500 |
2.500 |
5.000 |
5.000 |
10.000 |
25.000 |
installed power workspindle in kW: |
42 |
78 |
78 |
104 |
104 |
104 |
256 |
No. of workpiece spindles |
1 - 2 |
1 - 2 |
1 - 2 |
1 - 2 |
1 - 2 |
1 |
1 |
max. speed X-axis in m/min |
60 |
60 |
40 |
40 |
40 |
40 |
40 |
max. speed Z-axis in m/min |
30 |
30 |
24 |
24 |
24 |
24 |
24 |
Controller |
Sinumerik 840D |
Sinumerik 840D |
Sinumerik 840D |
Sinumerik 840D |
Sinumerik 840D |
Sinumerik 840D |
Sinumerik 840D |
Footprint basic machine |
4.000 x 2.600 |
4.300 x 2.600 |
4.700 x 2.600 |
5.200 x 3.200 |
5.600 x 3.200 |
6.400 x 3.800 |
9.600 x 7.000 |
Weight in t |
15 |
20 |
25 |
30 |
35 |
40 |
120 |
*Different workpiece geometries require more individual machine designs. For this reason, the technical data given here serve as a guide, but may deviate from reality in individual cases.